Polypropylene composite material and preparation method and application thereof
A composite material and polypropylene technology, applied in the field of 3D printing, can solve the problems of less printing materials, brittle products, and limited development, and achieve excellent 3D printing effects, high cross-section roundness, and good processing fluidity
- Summary
- Abstract
- Description
- Claims
- Application Information
AI Technical Summary
Benefits of technology
Problems solved by technology
Method used
Image
Examples
Embodiment 1
[0042] Proportion according to the following mass percentages:
[0043] Weigh 48 parts of homopolypropylene (brand: PPZ30S, China Coal Shaanxi Yulin Energy Chemical Co., Ltd.), 20 parts of copolymerized polypropylene (brand: PPK8009, China Petrochemical Corporation Guangzhou Branch), 5 parts of polylactic acid (brand : REVODE195, Zhejiang Hisun Biomaterials Co., Ltd.), 2 parts of polypropylene grafted maleic anhydride (brand: PC-1B, Foshan Nanhai Baichen Polymer New Materials Co., Ltd.) mixed and dried at 80°C for 4h get the first product;
[0044] Weigh 0.3 parts of white oil (brand name: FD4700, Foshan Daqing Linyuan Chemical Co., Ltd.) and add it to the first product, stir at a rotating speed of 1000r / min for 5min and add 15 parts of talc (mesh 1000 mesh), 0.1 part of Antioxidant 1010, 0.1 part of Antioxidant 168, 0.1 part of Calcium Stearate and 0.1 part of Light Stabilizer 770, and continue stirring for 10min at 1500r / min to obtain the second product;
[0045] The seco
Embodiment 2
[0048]Proportion according to the following mass percentages:
[0049] Weigh 55 parts of homopolypropylene (brand: PPZ30S, China Coal Shaanxi Yulin Energy Chemical Co., Ltd.), 15 parts of copolymerized polypropylene (brand: PPK8009, China Petrochemical Corporation Guangzhou Branch), 10 parts of polylactic acid (brand : REVODE195, Zhejiang Hisun Biomaterials Co., Ltd.), 5 parts of polypropylene grafted maleic anhydride (brand: PC-1B, Foshan Nanhai Baichen Polymer New Materials Co., Ltd.) were mixed and dried at 80 °C 4h to get the first product;
[0050] Weigh 0.3 parts of white oil (brand name: FD4700, Foshan Daqing Linyuan Chemical Co., Ltd.) and add it to the first product, and add 20 parts of barium sulfate (the mesh number is 1000 mesh) after stirring for 5 minutes at a rotating speed of 1000 r / min, 0.1 part of Antioxidant 1010, 0.1 part of Antioxidant 168, 0.1 part of Calcium Stearate and 0.1 part of Light Stabilizer 944, and continue stirring at 1500r / min for 10min to
Embodiment 3
[0054] Proportion according to the following mass percentages:
[0055] Weigh 50 parts of homopolypropylene (brand: PPZ30S, China Coal Shaanxi Yulin Energy Chemical Co., Ltd.), 10 parts of copolymerized polypropylene (brand: PPK8009, China Petrochemical Corporation Guangzhou Branch), 10 parts of polylactic acid (brand : REVODE195, Zhejiang Hisun Biomaterials Co., Ltd.), 5 parts of hydrogenated styrene-butadiene block copolymer grafted maleic anhydride (brand: TER-MS19, Ter Hong Kong Co., Ltd.) after mixing, at 80 ℃ The first product was obtained by drying under conditions for 4h;
[0056] Weigh 0.3 part of white oil (brand name: FD4700, Foshan Daqing Linyuan Chemical Co., Ltd.) into the first product, stir for 5min at a rotating speed of 1000r / min, add 15 parts of talcum powder (mesh 1000 mesh), 15 parts parts of barium sulfate (mesh 1000 mesh), 0.1 part of antioxidant 1010, 0.1 part of antioxidant 168, 0.1 part of calcium stearate and 0.1 part of light stabilizer 770, and con
PUM
Property | Measurement | Unit |
---|---|---|
Mesh | aaaaa | aaaaa |
Mesh | aaaaa | aaaaa |
Abstract
Description
Claims
Application Information
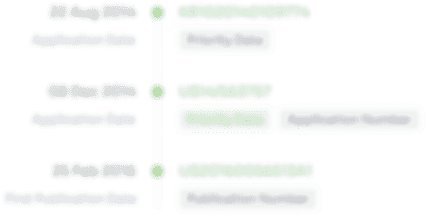
- R&D Engineer
- R&D Manager
- IP Professional
- Industry Leading Data Capabilities
- Powerful AI technology
- Patent DNA Extraction
Browse by: Latest US Patents, China's latest patents, Technical Efficacy Thesaurus, Application Domain, Technology Topic.
© 2024 PatSnap. All rights reserved.Legal|Privacy policy|Modern Slavery Act Transparency Statement|Sitemap