Composite microsphere with radial fibrous mesoporous shell layer/hollow nuclear layer structure and preparation method of composite microsphere
A composite microsphere and fibrous technology, which is applied in the preparation of microspheres and microcapsule preparations, can solve the problems of serious agglomeration of hollow microspheres, limit the application of hollow microspheres, and harsh synthesis conditions, and achieve adjustable performance, Ease of industrial production and improved performance of microspheres
- Summary
- Abstract
- Description
- Claims
- Application Information
AI Technical Summary
Benefits of technology
Problems solved by technology
Method used
Image
Examples
Embodiment 1
[0092] Add 6 g of styrene monomer to a three-necked flask filled with 100 mL of deionized water, stir mechanically at room temperature (250 rpm), and pass nitrogen gas for 30 min. When the temperature was raised to 70°C under a nitrogen atmosphere, 60mg of initiator KPS was added and reacted for 24h. The product was transferred to a centrifuge tube, centrifuged, washed with ethanol, centrifuged, and dried in a blast oven at 50°C for use. The product looks like figure 1 As shown, the average particle size is 967nm, and the polydispersity index (PDI) is 1.11.
[0093] Weigh 0.4g of cetyltrimethylammonium bromide (CTAB) into a 100mL round bottom flask, then add 20mL of water and 8mL of absolute ethanol into the flask. Weigh 450 mg of the prepared polystyrene microspheres into the flask, then add 1 mL of ammonia water, and stir at room temperature for 30 min. Add 500 μL TEOS dropwise to the system, and react at room temperature for 24 h under stirring conditions.
[0094] Subsequ
Embodiment 2
[0097] Prepare the composite microsphere with radial fibrous mesoporous shell / hollow core layer structure in the same manner as in Example 1, the difference is that the first polymerization reaction time for preparing the hollow core layer is 12 hours, and the prepared TEM photos of composite microspheres with radial fibrous mesoporous shell / hollow core structure see Image 6 , Figure 7 for Image 6 - Enlarged view of the composite microspheres in b, the average particle size of the corresponding composite microspheres is 1 μm.
Embodiment 3
[0099] Composite microspheres with a radial fibrous mesoporous shell / hollow core structure were prepared in the same manner as in Example 1, except that the organic solvent was replaced by n-hexane.
PUM
Property | Measurement | Unit |
---|---|---|
The average particle size | aaaaa | aaaaa |
Thickness | aaaaa | aaaaa |
Specific surface area | aaaaa | aaaaa |
Abstract
Description
Claims
Application Information
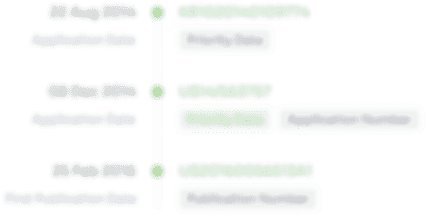
- R&D Engineer
- R&D Manager
- IP Professional
- Industry Leading Data Capabilities
- Powerful AI technology
- Patent DNA Extraction
Browse by: Latest US Patents, China's latest patents, Technical Efficacy Thesaurus, Application Domain, Technology Topic.
© 2024 PatSnap. All rights reserved.Legal|Privacy policy|Modern Slavery Act Transparency Statement|Sitemap