Medical dialysis body paper and production method thereof
A production method and technology for base paper, applied in pulp beating method, pulp beating/refining method, paper and other directions, can solve the problems of not containing fluorescent substances, low ash content, etc., and achieve good heat sealing and peeling effect, paper strength Good, reduce the effect of intermediate links
- Summary
- Abstract
- Description
- Claims
- Application Information
AI Technical Summary
Benefits of technology
Problems solved by technology
Method used
Image
Examples
Embodiment 1
[0036] Example 1, the trial formulation amount is 55g / m 2 The four experimental products A1, A2, A3 and A4:
[0037] The first product A1, the ratio of the pulp after the tapping of needles and the pulp after the tapping of broad leaves is 1:3, with 1.2% AKD sizing agent, 0.5% PPE wet strength agent, no guar gum dispersant, operating concentration 0.4 %, the amount of surface sizing agent is 0.5%;
[0038] The second product A2, the ratio of the pulp after knocking needles and the pulp after broadleaf knocking is 1:3, adding 1.3% AKD sizing agent, 0.6% PPE wet strength agent, 0.05% guar gum dispersant, and operating concentration 0.45 %, the amount of surface sizing agent 0.7%;
[0039] The third product A3, the ratio of the pulp after coniferous knocking and the pulp after broad-leaved knocking is 1:3, adding 1.4% AKD sizing agent, 0.5% to 0.8% PPE wet strength agent, 0.10% guar gum dispersant, Operating concentration is 0.5%, and the amount of surface sizing agent is 0.8%;
[0040]
Embodiment 2
[0045] Example 2: The trial formulation amount is 60g / m 2 The four experimental products B1, B2, B3 and B4:
[0046] The first product B1, the ratio of the pulp after the tapping of the needles and the pulp after the tapping of the broad leaves is 1:3, with 1.2% AKD sizing agent, 0.5% PPE wet strength agent, no guar gum dispersant, operating concentration 0.4 %, the amount of surface sizing agent is 0.5%;
[0047] The second product B2, the ratio of the pulp after knocking needles and the pulp after broad-leaf knocking is 1:3, adding 1.3% AKD sizing agent, 0.6% PPE wet strength agent, 0.05% guar gum dispersant, operating concentration 0.45 %, the amount of surface sizing agent 0.7%;
[0048] The third product B3, the ratio of the pulp after coniferous knocking and the pulp after broad-leaved knocking is 1:3, adding 1.4% AKD sizing agent, 0.5% to 0.8% PPE wet strength agent, 0.10% guar gum dispersant, Operating concentration is 0.5%, and the amount of surface sizing agent is 0.8%;
[
Embodiment 3
[0054] Example 3: The trial formulation amount is 65g / m 2 The four experimental products C1, C2, C3 and C4:
[0055] The first product C1, the ratio of the pulp after the tapping of needles and the pulp after the tapping of broad leaves is 1:3, with 1.2% AKD sizing agent, 0.5% PPE wet strength agent, no guar gum dispersant, operating concentration 0.4 %, the amount of surface sizing agent is 0.5%;
[0056] The second product C2, the ratio of the pulp after the tapping of needles and the pulp after the tapping of broad leaves is 1:3, adding 1.3% AKD sizing agent, 0.6% PPE wet strength agent, 0.05% guar gum dispersant, and operating concentration 0.45 %, the amount of surface sizing agent 0.7%;
[0057] The third product C3, the ratio of the pulp after the tapping of needles and the pulp after the tapping of broad leaves is 1:3, adding 1.4% AKD sizing agent, 0.5% to 0.8% PPE wet strength agent, 0.10% guar gum dispersant, Operating concentration is 0.5%, and the amount of surface sizin
PUM
Property | Measurement | Unit |
---|---|---|
Burst index | aaaaa | aaaaa |
Abstract
Description
Claims
Application Information
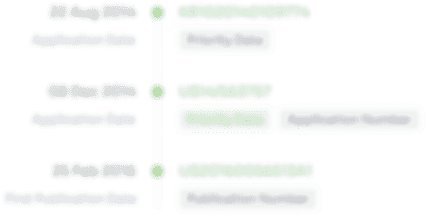
- R&D Engineer
- R&D Manager
- IP Professional
- Industry Leading Data Capabilities
- Powerful AI technology
- Patent DNA Extraction
Browse by: Latest US Patents, China's latest patents, Technical Efficacy Thesaurus, Application Domain, Technology Topic.
© 2024 PatSnap. All rights reserved.Legal|Privacy policy|Modern Slavery Act Transparency Statement|Sitemap