Preparation method of pre-buried method metal inner special-shaped bending hole
A pre-embedded and special-shaped technology, which is applied in the direction of mechanical equipment, heat exchange equipment, rotors, etc., can solve the problems of difficult machining and inability to process irregular holes, etc., and achieve the effects of cost saving, various types of metals, and wide sources
- Summary
- Abstract
- Description
- Claims
- Application Information
AI Technical Summary
Benefits of technology
Problems solved by technology
Method used
Examples
preparation example Construction
[0019] The preparation method of the special-shaped curved hole in the pre-embedded metal of the present invention is implemented according to the following steps:
[0020] Step 1, choose to make embedded metal pipes,
[0021] The material of the embedded metal pipe can be aluminum, copper, steel, magnesium, titanium or other metals; the material of the embedded metal pipe can be the same as the metal of the metal casting body, or it can be different from the metal casting body, so it can Insert inner holes of other materials to improve its wear resistance and corrosion resistance, such as inserting stainless steel and copper alloy pipes in ordinary cast steel and iron castings, and preparing inner holes of heterogeneous materials such as stainless steel and copper alloys in ordinary iron and steel parts hole, improve the corrosion resistance and wear resistance of the inner hole, and save costs. The cross-sectional shape of the embedded metal pipe can be any cross-sectional sha
Embodiment 1
[0029] Step 1, choose to make embedded metal pipe
[0030] The material of the embedded metal pipe is aluminum pipe, and the cross-sectional shape of the embedded metal pipe is like a triangle. The wall thickness is proportional to the thickness of the casting, and the wall thickness can be determined through simulation calculations. According to the shape and size requirements of the special-shaped bending hole in the metal part to be processed, the aluminum tube is placed in the pipe bending machine to be processed into a shape consistent with the required hole shape, and then cut to the required size.
[0031] Step 2, pretreatment of the embedded metal pipe
[0032] Descaling treatment, such as pickling, alkali washing, and sand blasting, is performed on the aluminum tube after the treatment in step 1, so as to remove the oxide skin layer on the outer surface of the aluminum tube. Use a grinder or emery cloth to roughen the surface of the aluminum tube, and then place the al
Embodiment 2
[0038] Step 1, choose to make embedded metal pipe
[0039] The material of the embedded metal pipe is selected as copper pipe, and the cross-sectional shape of the copper pipe is selected as square. The wall thickness of the copper pipe is proportional to the thickness of the casting, and the wall thickness of the copper pipe can be determined through simulation calculation. According to the shape and size requirements of the special-shaped bending hole in the metal part to be processed, the copper pipe is placed in the pipe bending machine to be processed into a shape consistent with the required hole shape, and then cut to the required size.
[0040] Step 2, pretreatment of the embedded metal pipe
[0041] Descaling treatment, such as pickling, alkali washing, and sand blasting, is performed on the copper pipes treated in step 1, so as to remove the oxide skin layer on the outer surface of the copper pipes. Use a grinder or emery cloth to roughen the surface of the copper tub
PUM
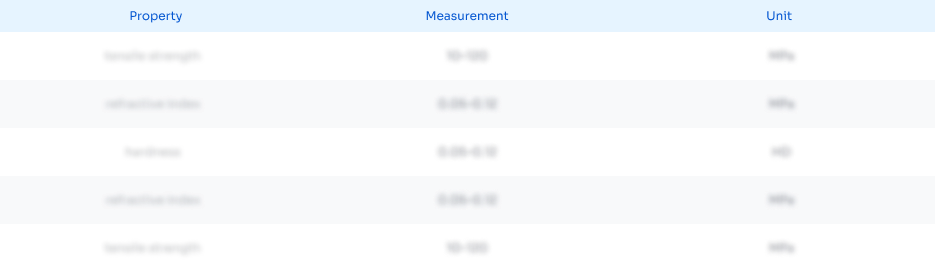
Abstract
Description
Claims
Application Information
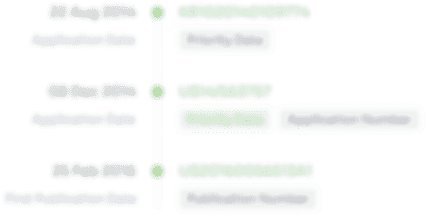
- R&D Engineer
- R&D Manager
- IP Professional
- Industry Leading Data Capabilities
- Powerful AI technology
- Patent DNA Extraction
Browse by: Latest US Patents, China's latest patents, Technical Efficacy Thesaurus, Application Domain, Technology Topic.
© 2024 PatSnap. All rights reserved.Legal|Privacy policy|Modern Slavery Act Transparency Statement|Sitemap