Environment-friendly flame-retardant textile fabric
A technology for textile fabrics and fabrics, which is applied in the directions of flame-retardant fibers, textiles and papermaking, and artificial filaments made of cellulose derivatives. performance, flame retardancy and other issues, to achieve good antibacterial effect, high regularity, and improve the effect of strength
- Summary
- Abstract
- Description
- Claims
- Application Information
AI Technical Summary
Problems solved by technology
Method used
Image
Examples
Embodiment 1
[0047] Antibacterial fiber is prepared by the following method:
[0048] (1) Add cellulose acetate into N,N-dimethylacetamide according to the solid-to-liquid ratio of 1g:20mL, stir at 150r / min at a constant temperature of 65°C to dissolve completely, add pyridine dropwise (the addition of pyridine The amount is 0.05% of the cellulose acetate mass);
[0049] (2) Transfer the above mixture to an ice-water bath, and when the temperature of the system drops to 0° C., slowly add sorbyl chloride dropwise under ice-water bath conditions (the amount of sorbyl chloride added is 40% of the cellulose acetate mass), and the dropwise After the last 15 minutes, the system was moved into a 65°C oil bath and stirred for 24 hours. After the reaction, the product was washed with deionized water and absolute ethanol until neutral to obtain modified acetate fiber;
[0050] (3) Dissolve modified cellulose acetate in N,N-dimethylacetamide, prepare a spinning solution with a mass fraction of 6%, an
Embodiment 2
[0052] (1) Add cellulose acetate into N,N-dimethylacetamide according to the solid-to-liquid ratio of 1g:20mL, stir at 150r / min at a constant temperature of 65°C to dissolve completely, add pyridine dropwise (the addition of pyridine The amount is 0.05% of the cellulose acetate mass);
[0053] (2) Transfer the above mixture to an ice-water bath, and when the temperature of the system drops to 0° C., slowly add sorbyl chloride dropwise under ice-water bath conditions (the amount of sorbyl chloride added is 40% of the cellulose acetate mass), and the dropwise After the last 15 minutes, the system was moved into a 65°C oil bath and stirred for 24 hours. After the reaction, the product was washed with deionized water and absolute ethanol until neutral to obtain modified acetate fiber;
[0054] (3) Dissolve modified cellulose acetate in N,N-dimethylacetamide, prepare a spinning solution with a mass fraction of 6%, and add cellulose acetate (the amount of cellulose acetate added is t
Embodiment 3
[0063] Flame retardant fibers are prepared by the following methods:
[0064] (1) Add terminal hydrogen-containing silicone oil and allylamine into a four-necked flask equipped with a thermometer, condenser, and magnetic stirrer according to the ratio of the amount of substances of 1:2.2, heat and stir slowly and raise the temperature to 50°C, Add catalyst chloroplatinic acid solution (the mass fraction of chloroplatinic acid solution is 6%, the mass of the added chloroplatinic acid solution is 0.1% of the total mass of terminal hydrogen-containing silicone oil and allylamine), then slowly heat up to 85°C, React for 4 hours, then obtain the flame retardant modifier through suction filtration and rotary evaporation;
[0065] (2) immerse the viscose fiber in an aqueous sulfuric acid solution with a mass fraction of 5%, soak it for 30 min at 40° C., then rinse the viscose fiber with distilled water until the lotion is neutral, and dry the viscose fiber to constant weight;
[0066]
PUM
Property | Measurement | Unit |
---|---|---|
Longitudinal tensile strength | aaaaa | aaaaa |
Longitudinal breaking strength | aaaaa | aaaaa |
Damage length | aaaaa | aaaaa |
Abstract
Description
Claims
Application Information
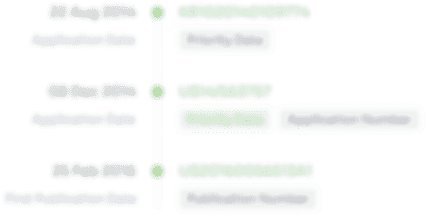
- R&D Engineer
- R&D Manager
- IP Professional
- Industry Leading Data Capabilities
- Powerful AI technology
- Patent DNA Extraction
Browse by: Latest US Patents, China's latest patents, Technical Efficacy Thesaurus, Application Domain, Technology Topic.
© 2024 PatSnap. All rights reserved.Legal|Privacy policy|Modern Slavery Act Transparency Statement|Sitemap