Method and device for high-temperature ultrahigh-pressure reheating waste heat power generation
A technology of waste heat power generation and ultra-high pressure, which is applied in the field of high-temperature and ultra-high pressure reheat waste heat power generation method and its device, can solve the problems of low energy utilization rate, achieve the effects of improving thermal cycle efficiency, low operating costs, and saving resources
- Summary
- Abstract
- Description
- Claims
- Application Information
AI Technical Summary
Problems solved by technology
Method used
Examples
Example Embodiment
[0031] Example 1
[0032] A high-temperature, ultra-high pressure reheating waste heat power generation method, such figure 1 As shown, including the following steps:
[0033] S1: Use the induced draft fan to send the 1000-1170℃ rising pipe high temperature flue gas generated during the production process of the coke production line to the high temperature and ultra-high pressure reheat waste heat boiler through the gas gathering pipe for heat exchange to produce 13.7MPa, 540℃ high temperature and ultra high pressure steam ;
[0034] S2: The 13.7MPa, 540℃ high-temperature and ultra-high pressure steam produced by the reheat waste heat boiler drives the operation of the pure condensing turbine, while the 0.4MPa, 152℃ low-pressure steam produced by the boiler is used for the deaerator of the waste heat boiler to deoxidize;
[0035] S3: The 2.9MPa and 350℃ steam produced by the high temperature and ultra-high pressure steam in the pure condensing turbine is sent to the boiler for reheating.
PUM
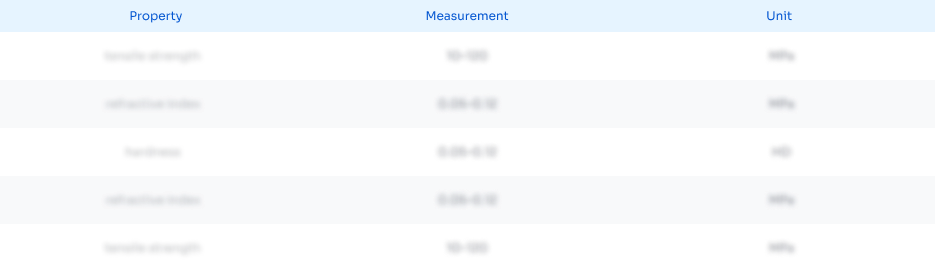
Abstract
Description
Claims
Application Information
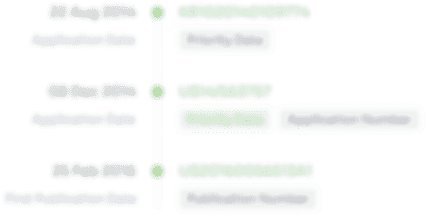
- R&D Engineer
- R&D Manager
- IP Professional
- Industry Leading Data Capabilities
- Powerful AI technology
- Patent DNA Extraction
Browse by: Latest US Patents, China's latest patents, Technical Efficacy Thesaurus, Application Domain, Technology Topic.
© 2024 PatSnap. All rights reserved.Legal|Privacy policy|Modern Slavery Act Transparency Statement|Sitemap