Cracking equipment
A technology of equipment and combustion cylinder, applied in the field of organic matter cracking, can solve the problems of low heat transfer efficiency, energy waste, unfavorable organic matter cracking, etc. Effect
- Summary
- Abstract
- Description
- Claims
- Application Information
AI Technical Summary
Benefits of technology
Problems solved by technology
Method used
Image
Examples
Embodiment Construction
[0027] The core of the invention is to provide a cracking equipment, which improves the heat transfer efficiency and reduces the waste of resources.
[0028] The following will clearly and completely describe the technical solutions in the embodiments of the present invention with reference to the accompanying drawings in the embodiments of the present invention. Obviously, the described embodiments are only some, not all, embodiments of the present invention. Based on the embodiments of the present invention, all other embodiments obtained by persons of ordinary skill in the art without making creative efforts belong to the protection scope of the present invention.
[0029] Please refer to Figure 1-Figure 6 , the embodiment of the present invention provides a kind of pyrolysis equipment, comprises cracking tube 1 and combustion tube 2, and combustion tube 2 is sheathed in the outer periphery of cracking tube 1, and cracking tube 1 rotates relative to fixed combustion tube 2;
PUM
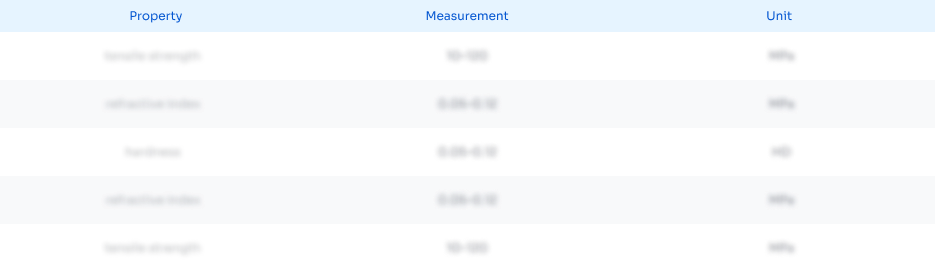
Abstract
Description
Claims
Application Information
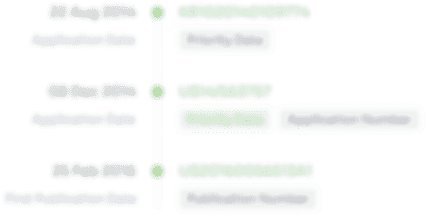
- R&D Engineer
- R&D Manager
- IP Professional
- Industry Leading Data Capabilities
- Powerful AI technology
- Patent DNA Extraction
Browse by: Latest US Patents, China's latest patents, Technical Efficacy Thesaurus, Application Domain, Technology Topic.
© 2024 PatSnap. All rights reserved.Legal|Privacy policy|Modern Slavery Act Transparency Statement|Sitemap