Multifunctional robot hand
A robotic hand and multi-functional technology, applied in the field of robotics, can solve problems such as the inability of robotic hands to adapt to special-shaped objects, and achieve the effects of improving firmness and reliability, increasing contact area, and increasing friction
- Summary
- Abstract
- Description
- Claims
- Application Information
AI Technical Summary
Benefits of technology
Problems solved by technology
Method used
Image
Examples
Embodiment 1
[0029] see Figure 1 to Figure 3 , the multifunctional robotic hand 1 includes a base 10 , fingers 20 and a drive assembly 30 , wherein the fingers 20 are movably connected to the bottom of the base 10 , and the drive assembly 30 is arranged on the base 10 for driving the fingers 20 to move. Specifically, a shape-adaptive component 40 is provided on the base 10, and the shape-adaptive component 40 is used to adapt to the outer contour of the object to be grasped, and can cooperate with the finger 20 to position the object to be grasped. One end of the shape-adaptive component 40 It can extend into the accommodation area formed around the fingers 20 . It can be understood that: the drive assembly 30 may include components such as motors, transmission gear sets, connecting rods, etc., and may also include components such as cylinders, air pipes, and air valves. Of course, according to specific conditions and needs, in other embodiments of the present invention Among them, the driv
Embodiment 2
[0040] see Figure 4 , the multifunctional robotic hand provided by the embodiment of the present invention is basically the same as that of Embodiment 1, except that the above-mentioned shape adaptive component 40 includes a soft rubber block 42, and the soft rubber block 42 is protruded from the bottom of the above-mentioned base 10 side. Specifically, the soft rubber block 42 has elasticity and plastic deformability, and when the soft rubber block 42 is squeezed by the object to be grasped, the outer contour of its bottom will be deformed to be consistent with the outer contour of the top of the object to be grasped, thereby making the soft rubber block The bottom surface of 42 is better engaged with the top surface of the object to be grasped, thereby increasing the contact area between the multifunctional robotic hand 1 and the object to be grasped.
[0041] Further, see Figure 4 , in the embodiment of the present invention, a plurality of second gas channels 421 are open
Embodiment 3
[0044] see Figure 5 , the multifunctional robotic hand provided by the embodiment of the present invention is basically the same as that of the first embodiment, except that the above-mentioned shape adaptive component 40 includes an air bag 43 protruding from the bottom side of the above-mentioned base 10 . Specifically, the airbag 43 has elasticity and plastic deformability. When the airbag 43 is squeezed by the object to be grasped, the outer contour of its bottom will be deformed to be consistent with the outer contour of the top of the object to be grasped, so that the bottom surface of the airbag 43 is better Engaging with the top surface of the object to be grasped, thereby increasing the contact area between the multifunctional robotic arm 1 and the object.
PUM
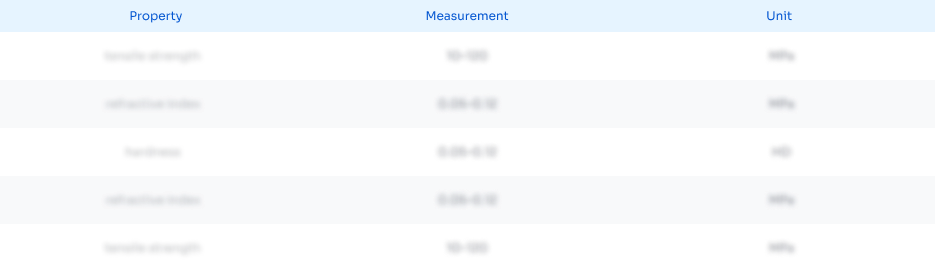
Abstract
Description
Claims
Application Information
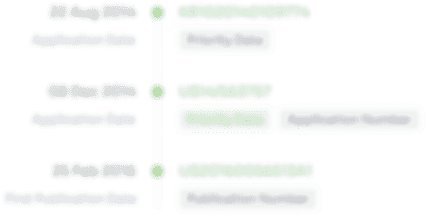
- R&D Engineer
- R&D Manager
- IP Professional
- Industry Leading Data Capabilities
- Powerful AI technology
- Patent DNA Extraction
Browse by: Latest US Patents, China's latest patents, Technical Efficacy Thesaurus, Application Domain, Technology Topic.
© 2024 PatSnap. All rights reserved.Legal|Privacy policy|Modern Slavery Act Transparency Statement|Sitemap