Raw material pressing device for producing a flame-retardant plastic-wood composite material
A technology of wood-plastic composite materials and pressing devices, which is applied in the field of raw material pressing devices for the production of flame-retardant wood-plastic composite materials, can solve the problems of inconvenient attachment of flame-retardant films, reduced production efficiency, and poor attachment effects, and achieves Convenient pressing, improved production efficiency, good effect
- Summary
- Abstract
- Description
- Claims
- Application Information
AI Technical Summary
Problems solved by technology
Method used
Image
Examples
Example Embodiment
[0023] Example
[0024] Such as Figure 1-6 As shown, the present invention provides a raw material pressing device for the production of flame-retardant plastic-wood composite materials, which includes a base 1, a supporting mechanism 2, a flame-retardant layer unwinding mechanism 3, a pressing mechanism 4, a cutting mechanism 5, and a placing mechanism 6. The supporting mechanism 2, the flame-retardant layer unwinding mechanism 3, the pressing mechanism 4, the cutting mechanism 5, and the placing mechanism 6 are all arranged on the top of the base 1, and the supporting mechanism 2 and the placing mechanism 6 are respectively arranged on the top of the base 1. At both ends, the flame-retardant layer unwinding mechanism 3 is arranged on the side of the supporting mechanism 2 close to the placing mechanism 6, and the pressing mechanism 4 is arranged on the side of the flame-retardant layer unwinding mechanism 3 close to the placing mechanism 6. The cutting mechanism 5 is arranged on
PUM
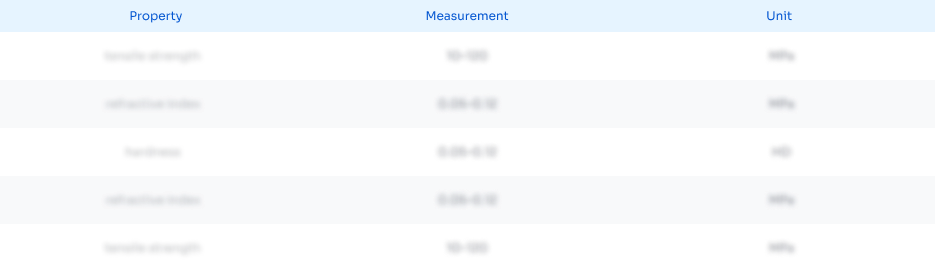
Abstract
Description
Claims
Application Information
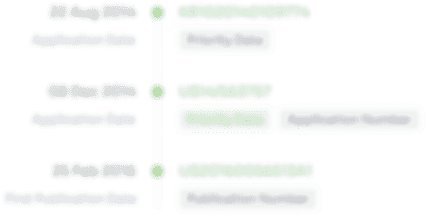
- R&D Engineer
- R&D Manager
- IP Professional
- Industry Leading Data Capabilities
- Powerful AI technology
- Patent DNA Extraction
Browse by: Latest US Patents, China's latest patents, Technical Efficacy Thesaurus, Application Domain, Technology Topic.
© 2024 PatSnap. All rights reserved.Legal|Privacy policy|Modern Slavery Act Transparency Statement|Sitemap