Aluminum alloy section character printing process
A technology of aluminum alloy profile and process, which is applied in the printing process, printing of special varieties of printed matter, printing, etc., can solve the problems of aluminum alloy profile printing process research, not in-depth, etc., to achieve strong printing adhesion, not easy to fall off, color and luster long-lasting effect
- Summary
- Abstract
- Description
- Claims
- Application Information
AI Technical Summary
Problems solved by technology
Method used
Examples
Embodiment 1
[0018] A printing process for aluminum alloy profiles, comprising the steps of:
[0019] 1): Printing: Put the printed paper and plastic film on the unwinding machine, print through the printing machine, then coat the polyurethane dissolved in acetone, and finally dry it. The printing environment temperature is 150°C ;
[0020] 2) Profile pretreatment: brush, degrease, water wash, pickle, and water wash the profile, and degrease: put the profile in a degreasing agent bath at 20°C, soak for 3 minutes, and keep stirring the degreasing agent, and then Take out the aluminum profile and pickle: put the profile in 10% dilute sulfuric acid for 10 minutes;
[0021] 3): Paste the characters: paste the plastic film with printed characters on the aluminum alloy profile, scrape it flat, squeeze out the air, make the plastic film and the surface of the aluminum alloy profile fit closely, after drying for 10 hours, put it into the baking oven Bake with medium heat, the temperature is 250°C,
Embodiment 2
[0024] A printing process for aluminum alloy profiles, comprising the steps of:
[0025] 1): Printing: Put the printed paper and plastic film on the unwinding machine, print through the printing machine, then coat the polyurethane dissolved in acetone, and finally dry it. The printing environment temperature is 155°C ;
[0026] 2) Profile pretreatment: scrub the profile, degrease, wash, pickle, and wash the profile, and degrease: put the profile into the degreasing agent bath at 20°C, soak for 4 minutes, and keep stirring the degreasing agent, and then Take out the aluminum profile and pickle: put the profile in 10% dilute sulfuric acid for 15 minutes;
[0027] 3): Paste the words: paste the printed plastic film on the aluminum alloy profile, scrape it flat, squeeze out the air, so that the plastic film and the surface of the aluminum alloy profile are closely attached, after drying for 11 hours, put it into the baking oven Bake with medium heat, the temperature is 300°C, the b
Embodiment 3
[0030] A printing process for aluminum alloy profiles, comprising the steps of:
[0031] 1): Printing: Put the printed paper and plastic film on the unwinding machine, print through the printing machine, then coat the polyurethane dissolved in acetone, and finally dry it. The printing environment temperature is 160°C ;
[0032] 2) Profile pretreatment: scrub the profile, degrease, wash, pickle, and wash the profile, and degrease: put the profile into the degreasing agent bath at 25°C, soak for 5 minutes, and keep stirring the degreasing agent, and then Take out the aluminum profile, pickling: put the profile into 10% dilute sulfuric acid and pickle for 20 minutes;
[0033] 3): Paste the words: paste the printed plastic film on the aluminum alloy profile, scrape it flat, squeeze out the air, make the plastic film and the surface of the aluminum alloy profile closely adhere, after drying for 12 hours, put it into the baking oven Bake with medium heat, the temperature is 300°C, th
PUM
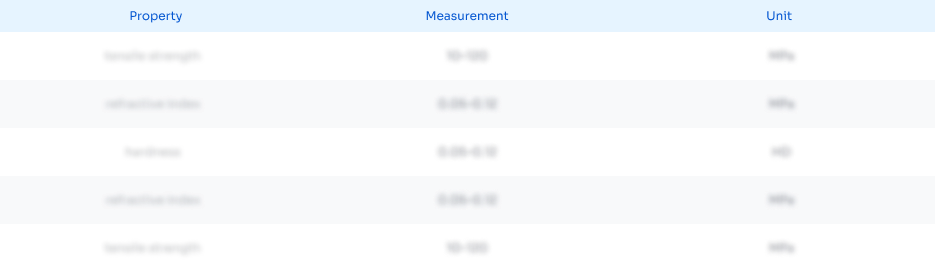
Abstract
Description
Claims
Application Information
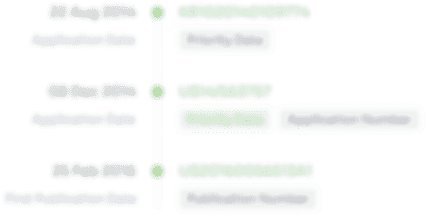
- R&D Engineer
- R&D Manager
- IP Professional
- Industry Leading Data Capabilities
- Powerful AI technology
- Patent DNA Extraction
Browse by: Latest US Patents, China's latest patents, Technical Efficacy Thesaurus, Application Domain, Technology Topic.
© 2024 PatSnap. All rights reserved.Legal|Privacy policy|Modern Slavery Act Transparency Statement|Sitemap