Production process of tea leaf carbon infrared heating environment-friendly fabric
A production process and tea technology, which is applied to the production process of tea carbon-infrared heating and environmentally friendly fabrics, can solve problems such as poor thermal insulation effect, and achieve the effects of fast coloring, improved dyeing process, and uniform dyeing.
- Summary
- Abstract
- Description
- Claims
- Application Information
AI Technical Summary
Problems solved by technology
Method used
Examples
Example Embodiment
[0017] Example 1
[0018] The production process of tea carbon infrared heating environmental protection fabrics is as follows: weaving→pretreatment→dying→dehydration→cutting→drying→setting→puffing, shearing→resetting→finished products;
[0019] (1) During weaving: the fabric is woven from 16S tea carbon fiber and 40S blended yarn on a 30-inch 20G Lida towel single jersey machine according to the flannel weaving method. The woven fabric weighs 230g / m 2 , The blended yarn is the veil, the tea carbon fiber is the terry yarn, and the blended yarn is made by blending cotton and polyester. The mass ratio of each component in the fabric is: tea carbon fiber accounts for 24.6%, cotton accounts for 45.24%, and polyester accounts for 30.16%. ;
[0020] (2) The pre-treatment adopts a gentle process, the steps are: water into the dyeing machine with a bath ratio of 1:8, then heat the water to 40°C, put it into the cloth, and then apply LOA-1 low temperature oxygen bleaching aid 2.5g / L, ZJ-
Example Embodiment
[0027] Example 2
[0028] The production process of tea carbon infrared heating environmental protection fabrics is as follows: weaving→pretreatment→dying→dehydration→cutting→drying→setting→puffing, shearing→resetting→finished products;
[0029] (1) Weaving: The fabric is woven from 12S tea carbon fiber and 36S blended yarn on a 30-inch 20G Lida towel single jersey machine according to the flannel weaving method. The woven fabric weighs 240g / m 2 , Blended yarn is a veil, tea carbon fiber is a terry yarn, blended yarn is made of cotton and polyester blended, the mass ratio of each component in the fabric is: tea carbon fiber accounts for 23.3%, cotton accounts for 46.6%, polyester accounts for 30.1% ;
[0030] (2) The pre-treatment adopts a gentle process, the steps are: water into the dyeing machine at a bath ratio of 1:8, then heat the water to 45°C, put it into the cloth, and then apply LOA-1 low temperature oxygen bleaching aid 3g / L, ZJ-CH60 Low temperature refining agent 1.5g
Example Embodiment
[0037] Example 3
[0038] The production process of tea carbon infrared heating environmental protection fabrics is as follows: weaving→pretreatment→dying→dehydration→cutting→drying→setting→puffing, shearing→resetting→finished products;
[0039] (1) During weaving: the fabric is woven from 18S tea carbon fiber and 32S blended yarn on a 30-inch 20G Lida towel single jersey machine according to the flannel weaving method. The woven fabric weighs 225g / m 2 , The blended yarn is the veil, the tea carbon fiber is the terry yarn, and the blended yarn is made by blending cotton and polyester. The mass ratio of each component in the fabric is: tea carbon fiber accounts for 23.95%, cotton accounts for 45.6%, and polyester accounts for 30.45%. ;
[0040] (2) The pre-treatment adopts a gentle process, the steps are: water into the dyeing machine with a bath ratio of 1:8, then heat the water to 35°C, put it into the cloth, and then apply LOA-1 low temperature oxygen bleaching aid 2g / L, ZJ-CH60
PUM
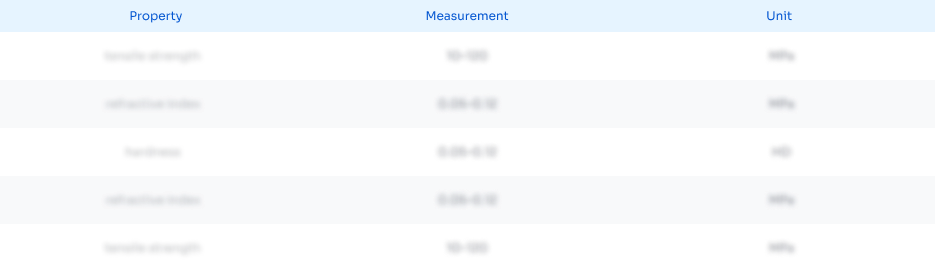
Abstract
Description
Claims
Application Information
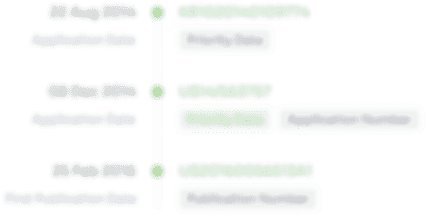
- R&D Engineer
- R&D Manager
- IP Professional
- Industry Leading Data Capabilities
- Powerful AI technology
- Patent DNA Extraction
Browse by: Latest US Patents, China's latest patents, Technical Efficacy Thesaurus, Application Domain, Technology Topic.
© 2024 PatSnap. All rights reserved.Legal|Privacy policy|Modern Slavery Act Transparency Statement|Sitemap