Method for preparing metal element doped cobalt oxide (Co3O4) nanofiber electrode by electrostatic spinning method
An electrospinning method and metal element technology, which is applied in the fields of materials science and engineering technology and chemistry, can solve the problems of poor controllability, low efficiency and low output, and achieve excellent catalytic performance, high yield and simple operation. Effect
- Summary
- Abstract
- Description
- Claims
- Application Information
AI Technical Summary
Problems solved by technology
Method used
Image
Examples
Embodiment 1
[0017] Molybdenum (Mo) doped cobalt oxide (Co 3 o 4 ) Preparation of nanofibers.
[0018] First, prepare organic polymer solution A: 0.6g of polyvinylpyrrolidone (PVP, molecular weight 130W) dissolved in 10ml of ethanol, followed by metal precursor solution B: 0.3g of cobalt nitrate hexahydrate (Co(NO 3 ) 2 ·6H 2 O) Dissolve in 3 g of water. Then prepare doped metal precursor solution C: 0.005g ammonium molybdate tetrahydrate ((NH 4 ) 6 Mo 7 o 24 4H 2 O) dissolved in 1 g of water. A, B, and C all need to be magnetically stirred for 1 hour, and then A, B, and C are mixed and stirred evenly to obtain spinning solution D.
[0019] Set the electrospinning parameters for spinning: positive voltage: 18Kv; negative voltage: 1.2Kv; flow rate: 0.15mm / min; receiving distance: 20cm; rotational speed: 200r / min.
[0020] The obtained fiber membrane was heat-treated in a muffle furnace at 500 °C for 2 h to obtain molybdenum (Mo)-doped cobalt oxide (Co 3 o 4 )Nanofibers.
Embodiment 2
[0022] Molybdenum (Mo) doped cobalt oxide (Co 3 o 4 ) Preparation of nanofibers.
[0023] First, prepare organic polymer solution A: 0.6g of polyvinylpyrrolidone (PVP, molecular weight 130W) dissolved in 10ml of ethanol, followed by metal precursor solution B: 0.15g of cobalt chloride hexahydrate (CoCl 2 ·6H 2 O) Dissolve in 3 g of water. Re-preparation of doped metal precursor solution C: 0.005g ammonium molybdate tetrahydrate (NH 4 ) 6 Mo 7 o 24 4H 2 O) dissolved in 1 g of water. A, B, and C all need to be magnetically stirred for 1 hour, and then A, B, and C are mixed and stirred evenly to obtain spinning solution D.
[0024] Set the electrospinning parameters for spinning: positive voltage: 18.2Kv; negative voltage: 1.4Kv; flow rate: 0.15mm / min; receiving distance: 22cm; rotational speed: 200r / min.
[0025] The obtained fiber membrane was heat-treated in a muffle furnace at 500 °C for 2 h to obtain molybdenum (Mo)-doped cobalt oxide (Co 3 o 4 )Nanofibers.
Embodiment 3
[0027] Molybdenum (Mo) doped cobalt oxide (Co 3 o 4 ) Preparation of nanofibers.
[0028] First, the preparation of organic polymer solution A: 0.6g of polyvinylpyrrolidone (PVP, molecular weight 130W) dissolved in 10ml of ethanol, followed by metal precursor solution B: 0.3g of cobalt acetylacetonate (Co(C 5 h 7 o 2 ) 3 ) was dissolved in 2 g of water. Then prepare doped metal precursor solution C: 0.005g ammonium molybdate tetrahydrate ((NH 4 ) 6 Mo 7 o 24 4H 2 O) dissolved in 1 g of water. A, B, and C all need to be magnetically stirred for 1 hour, and then A, B, and C are mixed and stirred evenly to obtain spinning solution D.
[0029] Set the electrospinning parameters for spinning: positive voltage: 18Kv; negative voltage: 1.2Kv; flow rate: 0.15mm / min; receiving distance: 20cm; rotational speed: 200r / min.
[0030] The obtained fiber membrane was heat-treated in a muffle furnace at 500 °C for 2 h to obtain molybdenum (Mo)-doped cobalt oxide (Co 3 o 4 )Nanof
PUM
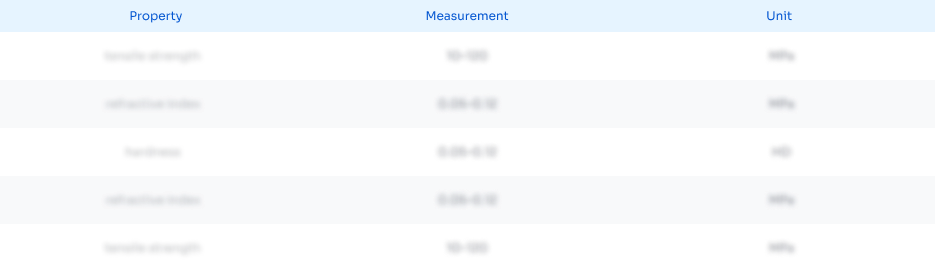
Abstract
Description
Claims
Application Information
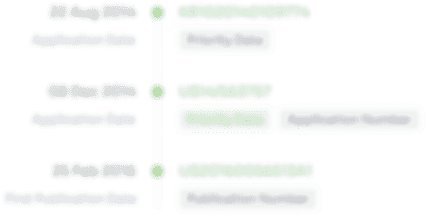
- R&D Engineer
- R&D Manager
- IP Professional
- Industry Leading Data Capabilities
- Powerful AI technology
- Patent DNA Extraction
Browse by: Latest US Patents, China's latest patents, Technical Efficacy Thesaurus, Application Domain, Technology Topic.
© 2024 PatSnap. All rights reserved.Legal|Privacy policy|Modern Slavery Act Transparency Statement|Sitemap