Carbon-coated sodium vanadium titanium fluorophosphate composite material and preparation and application thereof in sodium electricity
A technology of carbon-coated vanadium titanium sodium fluorophosphate and vanadium titanium sodium fluorophosphate is applied in the field of preparation of positive electrode materials for sodium ion batteries, which can solve the problems of unsatisfactory electrical properties of sodium ion battery composite materials, and reduce energy consumption and reduction. Excellent effect of time and electrochemical performance
- Summary
- Abstract
- Description
- Claims
- Application Information
AI Technical Summary
Problems solved by technology
Method used
Image
Examples
Example Embodiment
[0086] Example 1
[0087] This example uses a vanadium-titanium-titanium-titanium magnetite in Panzhihua, a 1.25 kg of vanadium-titanium-titanium magnetite, 0.1 kg of anhydrous sodium sulfate and 0.05 kg of organic binder (synthetic rubber; specifically terminal hydroxyl polybutiene) Polymer) After mixing into a 12 mm gabr, the ball is placed at a muffle furnace (air) for 45 minutes at 1100 ° C, and then removed from the cooler to 120 ° C. The bolt-baked ball was leached with 1.5L hot water, separated from the filter residue and filtrate, and the leaching solution was used to extract the production of vanadium. Crushed the filter residue to -250 specide from 75%, 0.2 kg of anthracite (leaching residue, the mass ratio of smokeless coal) added to the filter residue, mix uniform, and the group shifted into the bottom furnace (air) reduction 45 min Get high titanium slag and Zhuzhu steel. Further separation by the magnetic selection, high titanium residue is made of titanium sulfuric aci
Example Embodiment
[0088] Example 2
[0089] This example uses a vanadium-titanium-titanium-titanium magnetite in Panzhihua, a 1.25 kg of vanadium-titanium-titanium magnetite, 0.1 kg of anhydrous sodium sulfate and 0.05 kg of organic binder (synthetic rubber; specifically terminal hydroxyl polybutiene) The polymer) is mixed into a 12 mm gantle, and the ball is placed at a muffle furnace (air) at 1400 ° C for 45 minutes, and after cooling to 120 ° C by the cooler. The bolt-baked ball was leached with 1.5L hot water, separated from the filter residue and filtrate, and the leaching solution was used to extract the production of vanadium. Crushed the filter residue to -250 specide from 75%, 0.2 kg of anthracite (leaching residue, the mass ratio of smokeless coal) added to the filter residue, mix uniform, and the group shifted into the bottom furnace (air) reduction 45 min Get high titanium slag and Zhuzhu steel. Further separation by the magnetic selection, high titanium residue is made of titanium sulfuri
Example Embodiment
[0090] Example 3
[0091] This example uses a vanadium-titanium-titanium-titanium magnetite in Panzhihua, a 1.25 kg of vanadium-titanium-titanium magnetite, 0.1 kg of anhydrous sodium sulfate and 0.05 kg of organic binder (synthetic rubber; specifically terminal hydroxyl polybutiene) The polymer) is mixed into a 12 mm agglomerate, and the ball is placed at a muffle furnace (air) for 45 minutes at 1250 ° C, and after cooling it to 120 ° C by the cooler. The bolt-baked ball was leached with 1.5L hot water, separated from the filter residue and filtrate, and the leaching solution was used to extract the production of vanadium. Crushed the filter residue to -250 specide from 75%, 0.2 kg of anthracite (leaching residue, the mass ratio of smokeless coal), added to the filter residue, mix uniform and uniformly transferred into the bottom furnace at 1150 ° C (air) reduction 45min Get high titanium slag and Zhuzhu steel. Further separation by the magnetic selection, high titanium residue is m
PUM
Property | Measurement | Unit |
---|---|---|
Particle size | aaaaa | aaaaa |
Particle size | aaaaa | aaaaa |
Specific surface area | aaaaa | aaaaa |
Abstract
Description
Claims
Application Information
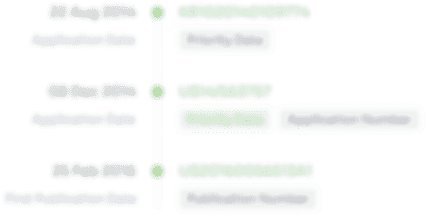
- R&D Engineer
- R&D Manager
- IP Professional
- Industry Leading Data Capabilities
- Powerful AI technology
- Patent DNA Extraction
Browse by: Latest US Patents, China's latest patents, Technical Efficacy Thesaurus, Application Domain, Technology Topic.
© 2024 PatSnap. All rights reserved.Legal|Privacy policy|Modern Slavery Act Transparency Statement|Sitemap