Diamond saw blade
A technology of diamond saw blades and diamond cutter heads, which is applied in the field of diamond tools, can solve the problems of poor bearing capacity, improper formula, uneven heat and force, etc., to improve service life and sharpness, meet multi-purpose requirements, and reduce invalidation wasteful effect
- Summary
- Abstract
- Description
- Claims
- Application Information
AI Technical Summary
Problems solved by technology
Method used
Image
Examples
preparation example Construction
[0046] (3) Preparation of diamond cutter head: Mix the raw materials of diamond cutter head according to the ratio, then cold press and sinter, and then hot press and sinter; when hot pressing and sintering, the sintering temperature is 790-850°C, and the pressure is 50-60kg / cm 2 , The holding time is 60 minutes; then use a grinder to sharpen and trim the saw blade.
[0047] (4) Cold-pressed connection: splicing the processed saw blade substrate and the diamond cutter head into the cold-pressed connection steel mold (because the size of the diamond cutter head is slightly larger than the gap between the teeth on the substrate, so the diamond cutter after splicing Only a part of the tapered shank of the head extends into the gap between the saw teeth); fix the assembled cold-pressed connection steel mold on the workbench, and then use a press to apply a force perpendicular to the diamond to both ends of the cold-pressed connection steel mold. The loading force F on the outer end
Embodiment 1
[0050] The process of preparing the diamond saw blade in this embodiment is:
[0051] 1. Press Figure 1-2 Design the diamond saw blade structure and process the substrate.
[0052] 2. The raw material of the diamond cutter head consists of (parts by weight): 25 parts of copper, 40 parts of iron, 15 parts of nickel, 5 parts of cobalt, 6 parts of tin, 9 parts of rare earth, 8 parts of WC powder; 0.8 part of liquid paraffin, 1.2 parts of diamond share.
[0053] Put the knife head raw material into the mixing tank and mix for 3 hours, then pour the powder into the mold for cold pressing, and then hot pressing and sintering. The hot pressing sintering temperature is 800°C and the pressure is 60kg / cm 2 , holding time 60 minutes. After hot pressing and sintering, the grinding wheel and abrasive belt are used to grind the cutter head. The prepared diamond segment has a uniform and dense structure, such as image 3 (a) shown. After testing, the hardness of the cutter head is 195
Embodiment 2
[0056] The process of preparing the diamond saw blade in this embodiment is:
[0057] 1. Press Figure 1-2 Design the diamond saw blade structure and process the substrate.
[0058] 2. The raw material of the diamond cutter head consists of (parts by weight): 26 parts of copper, 37 parts of iron, 16 parts of nickel, 5 parts of cobalt, 8 parts of tin, 7 parts of rare earth Y, 8 parts of WC powder, 0.7 part of liquid paraffin, Diamond 1.5 parts.
[0059] Put the knife head raw material into the mixing tank and mix for 3 hours, then pour the powder into the mold for cold pressing, and then hot pressing and sintering. The hot pressing sintering temperature is 805°C and the pressure is 60kg / cm 2 , holding time 60 minutes. After hot pressing and sintering, the grinding wheel and abrasive belt are used to grind the cutter head. The prepared diamond segment has a uniform and dense structure. After testing, the hardness of the cutter head is 194HB, and the mass wear loss of the al
PUM
Property | Measurement | Unit |
---|---|---|
Hardness | aaaaa | aaaaa |
Abstract
Description
Claims
Application Information
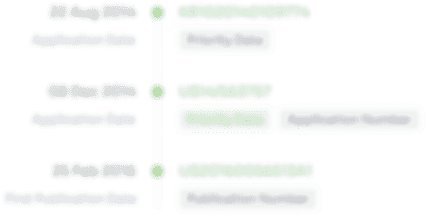
- R&D Engineer
- R&D Manager
- IP Professional
- Industry Leading Data Capabilities
- Powerful AI technology
- Patent DNA Extraction
Browse by: Latest US Patents, China's latest patents, Technical Efficacy Thesaurus, Application Domain, Technology Topic.
© 2024 PatSnap. All rights reserved.Legal|Privacy policy|Modern Slavery Act Transparency Statement|Sitemap