Preparation method of environment-friendly flame-retardant corrosion-resistant nano composite fiber base material
A nano-composite fiber and corrosion-resistant technology, applied in anti-corrosion coatings, coatings, etc., can solve problems such as harming people's health, affecting workers' health, and lack of surface coatings, and achieves good environmental performance, sustainable production, and economical reasonable effect
- Summary
- Abstract
- Description
- Claims
- Application Information
AI Technical Summary
Benefits of technology
Problems solved by technology
Method used
Image
Examples
Embodiment 1
[0043] see figure 1 , the present invention provides a technical solution: a method for preparing an environmentally friendly flame-retardant and corrosion-resistant nanocomposite fiber substrate, including some steps:
[0044] S1. Raw material preparation: take raw materials according to the following parts by weight: 50 parts of wood fiber, 10 parts of polyamide, 2 parts of glass fiber, 3 parts of adhesive, 2 parts of flame retardant, 40 parts of nano-coating;
[0045] S2. Raw material mixing: add raw material wood fiber, polyamide, glass fiber into the mixer by weight and mix for 6 minutes, with a rotating speed of 100 rpm;
[0046] S3. Raw material drying: send the wet fiber obtained in S2 into a dryer for drying, the drying inlet temperature is 140°C, and the drying outlet temperature is 50°C;
[0047] S4. Add viscose and flame retardant: add raw material viscose and flame retardant in the raw material after S3 treatment by weight, stir fully;
[0048] S5. Hot pressing for
Embodiment 2
[0075] see figure 1 , the present invention provides a technical solution: a method for preparing an environmentally friendly flame-retardant and corrosion-resistant nanocomposite fiber substrate, including some steps:
[0076] S1. Raw material preparation: take raw materials according to the following parts by weight: 100 parts of wood fiber, 20 parts of polyamide, 5 parts of glass fiber, 7 parts of adhesive, 5 parts of flame retardant, and 80 parts of nano-coating;
[0077] S2. Raw material mixing: add raw material wood fiber, polyamide, glass fiber by weight in the mixer and mix and stir for 10min at a speed of 100 rpm;
[0078] S3. Raw material drying: send the wet fiber obtained in S2 into a dryer for drying, the drying inlet temperature is 160°C, and the drying outlet temperature is 80°C;
[0079] S4. Add viscose and flame retardant: add raw material viscose and flame retardant in the raw material after S3 treatment by weight, stir fully;
[0080] S5. Hot pressing forming
PUM
Property | Measurement | Unit |
---|---|---|
Thickness | aaaaa | aaaaa |
Thickness | aaaaa | aaaaa |
Abstract
Description
Claims
Application Information
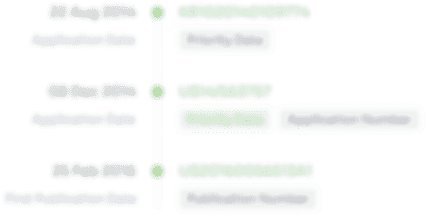
- R&D Engineer
- R&D Manager
- IP Professional
- Industry Leading Data Capabilities
- Powerful AI technology
- Patent DNA Extraction
Browse by: Latest US Patents, China's latest patents, Technical Efficacy Thesaurus, Application Domain, Technology Topic.
© 2024 PatSnap. All rights reserved.Legal|Privacy policy|Modern Slavery Act Transparency Statement|Sitemap