Steel wire product hot-dip galvanizing aluminum alloy production equipment and production process
A technology for steel wire products and production equipment, applied in hot dip plating process, metal material coating process, coating and other directions, can solve problems such as large energy consumption, and achieve the effect of reducing production water consumption and energy consumption
- Summary
- Abstract
- Description
- Claims
- Application Information
AI Technical Summary
Problems solved by technology
Method used
Image
Examples
Embodiment 1
[0030] A kind of hot-dip galvanized aluminum alloy production equipment for steel wire products (see attached figure 1), including a steel wire pay-off module 6, a steel wire ultrasonic cleaner 7, a tubular steel wire redox annealing furnace 1, a steel wire hot-dip galvanizing furnace 4, a steel wire hot-dip galvanized aluminum alloy furnace 5 and a steel wire take-up module 8. The steel wire on the line module is cleaned by the steel wire ultrasonic cleaner and sent to the tubular steel wire redox annealing furnace. Hot-dip galvanizing is carried out in the galvanizing furnace, and a hot-dip galvanizing alloy furnace is arranged behind the steel wire hot-dip galvanizing furnace, and a steel wire take-up module is arranged behind the steel wire hot-dip galvanizing alloy furnace. Among them, the tubular steel wire oxidation-reduction annealing furnace is separated into an oxidation furnace and a reduction furnace, and the oxide layer on the surface of the steel wire is reduced to
Embodiment 2
[0032] This embodiment is basically the same as Embodiment 1, the difference is that this embodiment (see attached figure 2 And attached Figure 4 ), also includes a steel wire activation and auxiliary plating pool 9, a steel wire activation and auxiliary plating pool is arranged behind the steel wire hot-dip galvanizing furnace, a steel wire hot-dip galvanizing and aluminum alloy furnace is arranged behind the steel wire activating and auxiliary plating pool, and a steel wire hot-dip galvanizing and The rear of the furnace is equipped with a steel wire take-up module, and the steel wire hot-dip galvanizing furnace, the steel wire activation auxiliary plating pool and the steel wire hot-dip galvanized aluminum alloy furnace are transported by the lifting wheel 45, and the steel wire hot-dip galvanizing furnace and the steel wire activation A steel wire wiping device 41 and a steel wire cooling control device 42 are arranged between the fluxing pools. The lifting wheel between t
Embodiment 3
[0036] This embodiment is basically the same as Embodiment 1, the difference is that this embodiment (see attached image 3 ) also includes a gas supply device 32, the hydrogen-nitrogen mixed gas charging device is equipped with a mixed gas valve 19 for controlling the flow rate of the hydrogen-nitrogen mixed gas, and each gas nozzle passes through a corresponding gas branch pipe and the gas main pipe The gas main pipe is connected with the gas supply device, and the gas main pipe is equipped with a gas valve 18 for controlling the flow of gas, and the mixed gas valve and the gas valve are both electromagnetic regulating valves. In this embodiment, a mixed gas valve is used to control the flow rate of the charged gas, and the pressure balance in the pipe is ensured through the mixed gas valve. Further, the independent control method of hydrogen input and nitrogen input can be used separately, and the independent input control is used to ensure the pressure balance in the pipe. Th
PUM
Property | Measurement | Unit |
---|---|---|
Length range | aaaaa | aaaaa |
Length | aaaaa | aaaaa |
Abstract
Description
Claims
Application Information
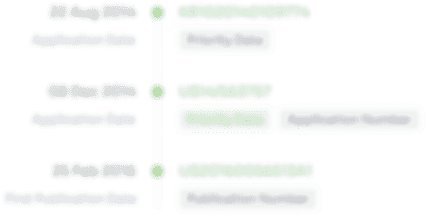
- R&D Engineer
- R&D Manager
- IP Professional
- Industry Leading Data Capabilities
- Powerful AI technology
- Patent DNA Extraction
Browse by: Latest US Patents, China's latest patents, Technical Efficacy Thesaurus, Application Domain, Technology Topic.
© 2024 PatSnap. All rights reserved.Legal|Privacy policy|Modern Slavery Act Transparency Statement|Sitemap