Leaching method of black shale uranium vanadium ore
A black shale and vanadium ore technology, applied in the field of uranium ore hydrometallurgy, can solve the problems of high consumption of reagents, excessive iron in vanadium products, high dosage of alkali and reducing agent, etc., to reduce raw material consumption, inhibit iron dissolution, and reduce leaching surplus Effect of Acid Concentration
- Summary
- Abstract
- Description
- Claims
- Application Information
AI Technical Summary
Problems solved by technology
Method used
Image
Examples
Embodiment 1
[0048] A black shale uranium-vanadium ore contains 1.05% vanadium and 0.085% uranium, of which 82% vanadium exists in mica, and uranium mainly exists in the form of adsorption. The black shale uranium vanadium ore is processed by the following steps:
[0049] (1) Ore pretreatment: the ore is ground until the particle size is -60 mesh, adding 20wt% (in raw ore mass) sulfuric acid, 15wt% (in raw ore mass) water, and mixing uniformly;
[0050] (2) Ripening: After the materials are mixed and sealed, heat-preserve and ripen at 90°C for 24 hours.
[0051] (3) Leaching: add water to the material after aging in the above step (2), control the liquid-solid volume mass ratio to 1, and carry out leaching at 96°C, add inhibitor sodium sulfate 1.2wt% during the leaching process, and add calcium hydroxide to adjust the leaching The process pH is 1.66, the dosage of calcium hydroxide is 3.89wt%, and the leaching time is 2h.
[0052] (4) Filtration: the pulp after leaching in the above step (3
Embodiment 2
[0058] A black shale uranium-vanadium ore contains 0.946% vanadium and 0.080% uranium, of which 88% vanadium exists in mica, and uranium mainly exists in the form of adsorption. The black shale uranium vanadium ore is processed by the following steps:
[0059] (1) Ore pretreatment: grind the ore until the particle size is -100 mesh, add 12%wt (based on raw ore mass) sulfuric acid, 18%wt (based on raw ore mass) water, and mix well.
[0060] (2) Ripening: After the materials are mixed and sealed, heat-preserve and ripen at 93°C for 2.5 hours.
[0061] (3) Leaching: Add water to the material after aging in the above step (2), control the liquid-solid volume mass ratio to be 1, and carry out leaching at 90°C, add inhibitor sodium sulfate 1.5wt% (calculated as raw ore) during the leaching process, and add Calcium carbonate regulates the pH of the leaching process to be 1.32, the consumption of calcium carbonate is 4.10wt% (based on raw ore), and the leaching time is 1h.
[0062] (4)
PUM
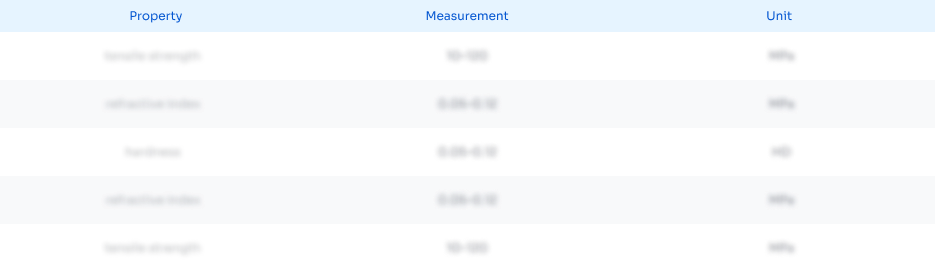
Abstract
Description
Claims
Application Information
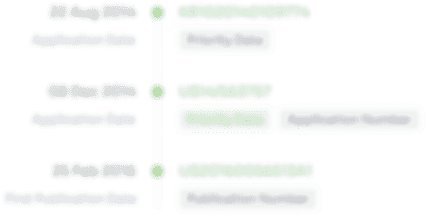
- R&D Engineer
- R&D Manager
- IP Professional
- Industry Leading Data Capabilities
- Powerful AI technology
- Patent DNA Extraction
Browse by: Latest US Patents, China's latest patents, Technical Efficacy Thesaurus, Application Domain, Technology Topic.
© 2024 PatSnap. All rights reserved.Legal|Privacy policy|Modern Slavery Act Transparency Statement|Sitemap