Method for preparing sodium antimonate from antimony oxide ore via alkaline approach
A technology for preparing sodium antimonate and antimony oxide is applied in the direction of improving process efficiency, which can solve the problem of low recovery rate and achieve the effects of less environmental pollution, non-toxic and harmless waste residue, and high recovery rate
- Summary
- Abstract
- Description
- Claims
- Application Information
AI Technical Summary
Problems solved by technology
Method used
Examples
Embodiment 1
[0025] This embodiment includes the following steps:
[0026] (1) Antimony oxide ore leaching: crush antimony oxide ore to -150 mesh, take -150 mesh antimony oxide ore 100g (including Sb10.15wt%, As0.15wt%, Pb1.02wt%, Fe17.02wt%), add Add 1.5g of hydrazine sulfate to 1.1L sodium hydroxide solution (NaOH concentration is 300.2g / L), leaching temperature is 82±2℃, and leaching time is 60 minutes; then filter to obtain filter residue, which weighs 82g after drying (of which Sb0.51 %, Fe20.55%), filtrate 1.0L (of which Sb9.73g / L);
[0027] (2) Purification of filtrate: Add 2.0 g of copper sulfate to the filtrate obtained in step (1), stir for 30 minutes at room temperature, and filter to obtain 1.0 L of purified liquid and purified residue; the dry weight of the obtained purified residue is 3.0 g (Sb0.04%, Cu21.23%);
[0028] (3) Oxidation of the purification solution: raise the temperature of the purification solution to 62±2°C, add 30mL of hydrogen peroxide (mass concentration:...
Embodiment 2
[0031] This embodiment includes the following steps:
[0032] (1) Antimony oxide ore leaching: crush antimony oxide ore to -150 mesh, take -150 mesh antimony oxide ore 200g (including Sb16.45%, As0.25%, Pb2.51%, Fe16.73%), add 2.5L sodium hydroxide solution (NaOH content is 383.5g / L) leaching, adding 5.9g of hydrazine hydrate, leaching temperature 87±2℃, leaching time 70 minutes, and then filtering to obtain a filter residue, the weight after drying is 150g (of which Sb0.33 %, Fe22.15%), filtrate 2.3L (of which Sb14.21g / L);
[0033] (2) Purification of filtrate: Add 8.2 g of copper chloride to the filtrate obtained in step (1), stir and purify for 35 minutes at room temperature, filter to obtain 2.3 L of purified liquid and purified slag, the dry weight of which is 4.9 g (Sb0.08% , Cu55.08%);
[0034] (3) Oxidation of the purification solution: heat up the purification solution obtained in step (2) to 72±2°C, add 118mL of hydrogen peroxide (60wt% mass concentration), oxidize...
Embodiment 3
[0037] This embodiment includes the following steps:
[0038] (1) Antimony oxide ore leaching: crush antimony oxide ore to -150 mesh, take -150 mesh antimony oxide ore 250g (including Sb13.59%, As0.35%, Pb2.68%, Fe18.79%), add Leach in 3.4L sodium hydroxide solution (NaOH concentration is 358.9g / L), add 6.8g hydrazine hydrate, leaching temperature 95±2℃, leaching time 90 minutes, then filter to obtain filter residue, weight after drying is 195g (of which Sb0.56%, Fe23.85%), filtrate 3.1L (of which Sb10.65g / L);
[0039] (2) Purification of the filtrate: add 10.2 g of copper sulfate to the filtrate obtained in step (1), purify for 45 minutes under stirring at room temperature, and filter to obtain a purified residue with a dry weight of 8.5 g (Sb0.06%, Cu35.83%) , purification solution 3.1L;
[0040](3) Oxidation of the purification solution: heat up the purification solution obtained in step (2) to 82±2°C, add 139 mL of hydrogen peroxide (mass concentration: 27.5wt%), oxidize...
PUM
Property | Measurement | Unit |
---|---|---|
rate of recovery | aaaaa | aaaaa |
rate of recovery | aaaaa | aaaaa |
evaporation rate | aaaaa | aaaaa |
Abstract
Description
Claims
Application Information
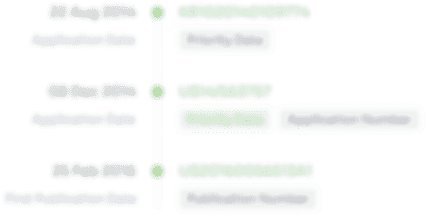
- R&D Engineer
- R&D Manager
- IP Professional
- Industry Leading Data Capabilities
- Powerful AI technology
- Patent DNA Extraction
Browse by: Latest US Patents, China's latest patents, Technical Efficacy Thesaurus, Application Domain, Technology Topic.
© 2024 PatSnap. All rights reserved.Legal|Privacy policy|Modern Slavery Act Transparency Statement|Sitemap