Preparation method of paper cup raw paper
一种制作工艺、原纸的技术,应用在纸浆原料添加过程、造纸、造纸机等方向,能够解决挺硬不容易、回用纤维性能衰减、纤维不易吸水润胀等问题,达到滤水性好、防止纤维角质化、提高松厚度的效果
- Summary
- Abstract
- Description
- Claims
- Application Information
AI Technical Summary
Problems solved by technology
Method used
Examples
Embodiment 1
[0022] 1) Pulping: including the manufacture of surface layer, bottom layer and core layer three-layer slurry, the surface layer slurry is made of the following raw materials in weight percentage: LBKP 70%, NBKP 30%; the bottom layer slurry is made of the following raw materials in weight percentage Made: LBKP65%, NBKP 35%; the core layer slurry is made of the following raw materials in parts by weight: LBKP 20%, NBKP 15%, APMP65%; the bulk thickness of the APMP pulp is 3.5cm 3 / g, tensile strength 14N·m / g; add a mass fraction of 3% ferrous nitrate solution to each layer of slurry, the amount of ferrous nitrate solution added is 5g / t slurry, mix and stir, and the ultrasonic power is 10W Under treatment for 30s.
[0023] 2) Seasoning: including filling, adding talc powder and mineral fiber to the core layer slurry, the total amount of talc powder and mineral fiber added is 150kg / t core layer slurry, and the weight ratio of talc powder to mineral fiber is 2:1. It also includes ...
Embodiment 2
[0026] 1) pulping: including the manufacture of surface layer, bottom layer and core layer three-layer slurry, the surface layer slurry is made of the following raw materials in weight percentage: LBKP 75%, NBKP 25%; the bottom layer slurry is made of the following raw materials in weight percentage Made: LBKP70%, NBKP 30%; the core layer slurry is made of the following raw materials in parts by weight: LBKP 30%, NBKP 10%, APMP60%; the bulk thickness of the APMP pulp is 3.7cm 3 / g, tensile strength 16N m / g; add a mass fraction of 6% ferrous nitrate solution to each layer of slurry, the amount of ferrous nitrate solution added is 10g / t slurry, mix and stir, and the ultrasonic power is 50W Down processing 120s.
[0027] 2) Seasoning: including filling, adding talc powder and mineral fiber to the core layer slurry, the total amount of talc powder and mineral fiber added is 200kg / t core layer slurry, and the weight ratio of talc powder to mineral fiber is 4:1. It also includes si...
Embodiment 3
[0030] 1) pulping: including the manufacture of surface layer, bottom layer and core layer three layers of slurry, the surface layer is made of the following slurry by weight percentage: LBKP 72%, NBKP 28%; the bottom layer is made of the following slurry by weight percentage Made: LBKP68%, NBKP32%; The core layer is made of the following slurry by weight: LBKP 25%, NBKP10%, APMP 65%; The bulk thickness of the APMP slurry is 3.6cm 3 / g, tensile strength 15N m / g; add ferrous nitrate solution with a mass fraction of 5% in each layer of slurry, the amount of ferrous nitrate solution added is 8g / t slurry, mix and stir, and the ultrasonic power is 30W Next process for 90s.
[0031] 2) Seasoning: including filling, adding talc powder and mineral fiber to the core layer slurry, the total amount of talc powder and mineral fiber added is 180kg / t core layer slurry, and the weight ratio of talc powder to mineral fiber is 3:1. It also includes sizing. The sizing is to add rosin and alumi...
PUM
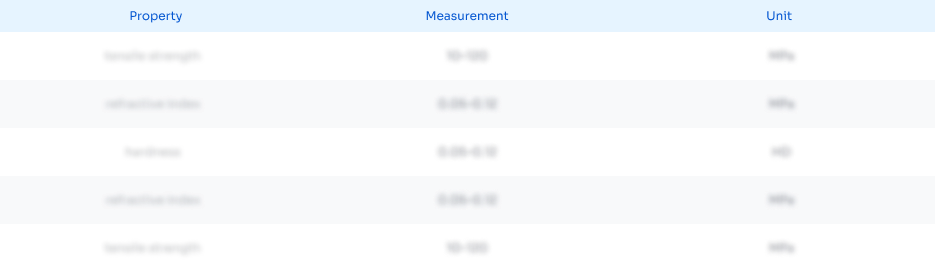
Abstract
Description
Claims
Application Information
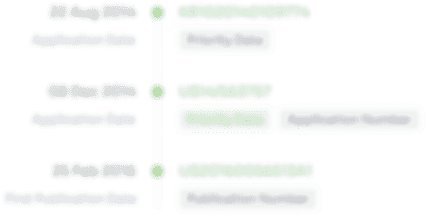
- R&D Engineer
- R&D Manager
- IP Professional
- Industry Leading Data Capabilities
- Powerful AI technology
- Patent DNA Extraction
Browse by: Latest US Patents, China's latest patents, Technical Efficacy Thesaurus, Application Domain, Technology Topic.
© 2024 PatSnap. All rights reserved.Legal|Privacy policy|Modern Slavery Act Transparency Statement|Sitemap