Coreless bottom line winding and shaping automatic all-in-one machine and method thereof
An all-in-one machine and bottom thread technology, applied in embroidery machines, embroidery machine mechanisms, textiles and papermaking, etc., can solve problems such as the inability to synchronize winding and shaping, the difficulty of initial winding of new coils, and the reduction of winding efficiency. The effect of high fixed cost, avoidance of manual operation errors, and increased utilization
- Summary
- Abstract
- Description
- Claims
- Application Information
AI Technical Summary
Problems solved by technology
Method used
Image
Examples
Embodiment
[0047] Such as Figures 1 to 9 As shown, a coreless bobbin thread winding and shaping automatic integrated machine is characterized in that it includes a frame 1 and two groups of bobbin thread pretreatment devices arranged on the frame 1, a spindle winding device, a back and forth cycloid transmission device, Winding pressing plate 6 constant force and thread cutting device and winding pushing device, as well as a set of bottom thread shaping device and a set of unloading device; can complete two sets of winding at the same time, and complete winding shaping on different groups alternately, Compact structure. A power distribution box 2 is arranged on one side of the rack 1 . The upper side of the frame 1 is provided with a vertically arranged installation shaft, and the coil 3 of winding is arranged on the installation shaft and can rotate.
[0048] The bottom line pretreatment device includes a dipping pool 4, and the bottom line is pretreated in the dipping pool 4; the oppos
PUM
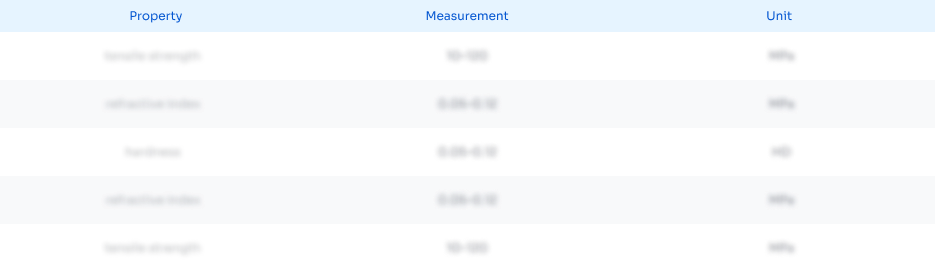
Abstract
Description
Claims
Application Information
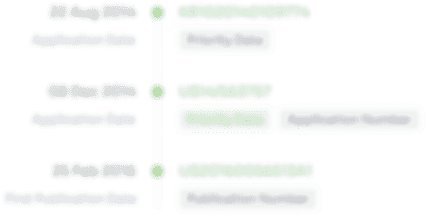
- R&D Engineer
- R&D Manager
- IP Professional
- Industry Leading Data Capabilities
- Powerful AI technology
- Patent DNA Extraction
Browse by: Latest US Patents, China's latest patents, Technical Efficacy Thesaurus, Application Domain, Technology Topic.
© 2024 PatSnap. All rights reserved.Legal|Privacy policy|Modern Slavery Act Transparency Statement|Sitemap