Novel swing welding track planning method for welding robot
A welding robot and trajectory planning technology, applied in welding equipment, auxiliary welding equipment, welding/cutting auxiliary equipment, etc., can solve the problems of welding quality influence, speed and acceleration step, etc., and achieve improved weld quality, continuous acceleration, The effect of continuous angular acceleration
- Summary
- Abstract
- Description
- Claims
- Application Information
AI Technical Summary
Benefits of technology
Problems solved by technology
Method used
Image
Examples
Embodiment Construction
[0090] The present invention will be described in further detail below according to the drawings and embodiments. The described embodiments are only some, not all, embodiments of the present invention. Based on the embodiments of the present invention, all other embodiments obtained by persons of ordinary skill in the art without creative efforts fall within the protection scope of the present invention.
[0091] This method first needs to determine the welding parameters and obtain the teaching point parameters; then determine the swing plane, and obtain the parameters required for interpolation through the speed planning of the entire trajectory in the weld coordinate system; then according to the idea of trajectory superposition , the cycloid trajectory planning method is adopted in the direction perpendicular to the weld seam, and the isochronous linear trajectory planning method is adopted along the weld seam direction. The plan is as follows:
[0092] A novel weaving we
PUM
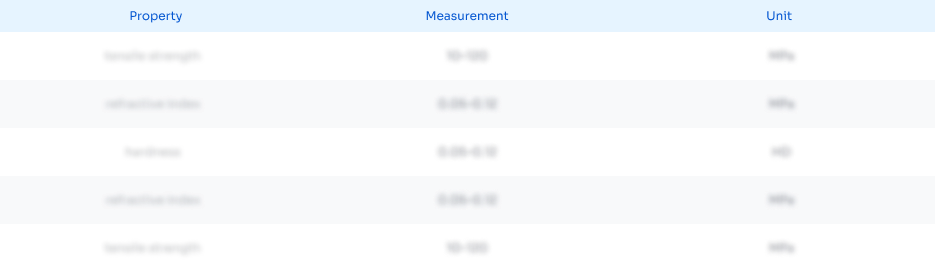
Abstract
Description
Claims
Application Information
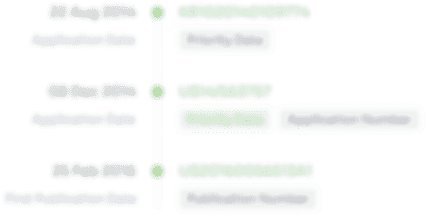
- R&D Engineer
- R&D Manager
- IP Professional
- Industry Leading Data Capabilities
- Powerful AI technology
- Patent DNA Extraction
Browse by: Latest US Patents, China's latest patents, Technical Efficacy Thesaurus, Application Domain, Technology Topic.
© 2024 PatSnap. All rights reserved.Legal|Privacy policy|Modern Slavery Act Transparency Statement|Sitemap