Preparation method of porous high-load electrode for lithium-sulfur battery
A lithium-sulfur battery and electrode technology, applied in battery electrodes, electrode manufacturing, lithium batteries, etc., can solve the problems of ineffective use of active materials in the inner layer, inability of electrolyte to infiltrate active materials, and unfavorable energy density of lithium-sulfur batteries. The effect of enriching the electrochemical reaction interface, improving ionic conductivity, and shortening the production time
- Summary
- Abstract
- Description
- Claims
- Application Information
AI Technical Summary
Benefits of technology
Problems solved by technology
Method used
Image
Examples
Embodiment 1
[0039] A method for preparing a porous high-capacity positive electrode for lithium-sulfur batteries, the process flow can be found in figure 1 , including the following steps:
[0040] 1) Preparation of sulfur-carbon film layer: first prepare sulfur-carbon mixture (sublimated sulfur-ketjen black), the specific operation is to put sublimated sulfur and ketjen black into a powder machine with a mass ratio of 4:1 and mix them evenly. about 15s each time, 3 times in total; then put it into the reaction kettle, vacuum seal it, place it in a blast drying oven, melt it at 155°C for 12 hours, take it out, and set it aside for use. Sulfur-carbon mixture (8.90g), conductive agent Ketjen black (0.5g), ethanol (30mL), NH 4 HCO 3 (with a particle size of 0.1-0.3 mm) was added into a planetary mixer, started the planetary mixer and stirred at a speed of 600 rpm for 3 hours until the slurry was uniform, and then stopped stirring to obtain an initial slurry. Then add binder (60wt.% PTFE emul
Embodiment 2
[0044] A method for preparing a porous high-capacity positive electrode for lithium-sulfur batteries. The difference from Example 1 is that the pore-forming agent NH 4 HCO 3 The content of the sulfur-carbon film layer prepared in step (1) is 20wt.% of the sum of the mass of the sulfur-carbon mixture, binder and conductive agent. All the other steps are consistent with Example 1.
Embodiment 3
[0046] A method for preparing a porous high-capacity positive electrode for lithium-sulfur batteries. The difference from Example 1 is that the pore-forming agent NH 4 HCO 3 The content of the sulfur-carbon film layer prepared in the step (1) is 30wt.% of the sum of the mass of the sulfur-carbon mixture, binder and conductive agent. All the other steps are consistent with Example 1.
PUM
Property | Measurement | Unit |
---|---|---|
Particle size | aaaaa | aaaaa |
Thickness | aaaaa | aaaaa |
Energy density | aaaaa | aaaaa |
Abstract
Description
Claims
Application Information
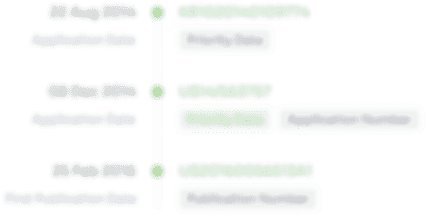
- R&D Engineer
- R&D Manager
- IP Professional
- Industry Leading Data Capabilities
- Powerful AI technology
- Patent DNA Extraction
Browse by: Latest US Patents, China's latest patents, Technical Efficacy Thesaurus, Application Domain, Technology Topic.
© 2024 PatSnap. All rights reserved.Legal|Privacy policy|Modern Slavery Act Transparency Statement|Sitemap