Fiber-reinforced high-strength foam concrete as well as preparation method and application thereof
A foam concrete and fiber-reinforced technology, applied in the field of building materials, can solve the problems of unusable load-bearing components, low flexural strength, narrow application range, etc., and achieve the effects of strong compactness, good thermal insulation effect, and low water absorption
- Summary
- Abstract
- Description
- Claims
- Application Information
AI Technical Summary
Problems solved by technology
Method used
Image
Examples
Embodiment 1
[0023] This embodiment provides a fiber-reinforced high-strength foam concrete, the raw materials of which include: 50 kg of ordinary Portland cement, 5 kg of silica fume, 10 kg of mineral powder, 5 kg of stainless steel slag powder, 70 kg of quartz sand, 5 kg of polypropylene fiber, and a composite admixture 1kg, blowing agent 5kg, water 50kg, described quartz sand is made up of four kinds of continuously graded quartz sands, and component and percentage by weight are respectively 10-20 mesh quartz sand 42.9%, 20-40 mesh quartz sand 21.4%, 23.8% of 40-80 mesh quartz sand, 11.9% of 80-120 mesh quartz sand, the composite admixture includes: 71% of water reducer, 12% of thickener, 17% of foam stabilizer. The water reducer is a polycarboxylate water reducer, the thickener is a cellulose thickener, the foam stabilizer is a modified silicone amide, the mineral powder is S95 mineral powder, and the specific surface area is 700m 2 / kg, the surface area of the stainless steel slag po
Embodiment 2
[0025] This embodiment provides a fiber-reinforced high-strength foam concrete, the raw materials of which include: 100kg of ordinary Portland cement, 10kg of silica fume, 20kg of mineral powder, 10kg of stainless steel slag powder, 60kg of quartz sand, 5kg of polypropylene fiber, and a composite admixture 2kg, blowing agent 5kg, water 40kg, described quartz sand is made up of four kinds of continuously graded quartz sands, and component and percentage by weight are respectively 10-20 mesh quartz sand 47.3%, 20-40 mesh quartz sand 15.9%, 24.1% of 40-80 mesh quartz sand, 12.7% of 80-120 mesh quartz sand, the composite admixture includes: 71% of water reducer, 12% of thickener, 17% of foam stabilizer. The water reducer is a polycarboxylate water reducer, the thickener is a cellulose thickener, the foam stabilizer is a modified silicone amide, the mineral powder is S105 mineral powder, and the specific surface area is 500m 2 / kg, the surface area of the stainless steel slag powd
Embodiment 3
[0027] This embodiment provides a fiber-reinforced high-strength foam concrete, the raw materials of which include: 50kg of ordinary Portland cement, 20kg of silica fume, 30kg of mineral powder, 10kg of stainless steel slag powder, 70kg of quartz sand, 1kg of polypropylene fiber, and a composite admixture 1.5kg, foaming agent 2kg, water 23kg, the quartz sand is composed of four kinds of continuously graded quartz sand, the components and weight percentages are 45% of 10-20 mesh quartz sand and 19.3% of 20-40 mesh quartz sand , 25% of 40-80 mesh quartz sand, 10.7% of 80-120 mesh quartz sand, and the composite admixture comprises by weight percentage: 71% of water reducer, 12% of thickener, and 17% of foam stabilizer. The water reducer is a polycarboxylate water reducer, the thickener is a cellulose thickener, the foam stabilizer is a modified silicone amide, and the foaming agent is a vegetable foaming agent. The mineral powder mentioned above is S95 mineral powder with a specific
PUM
Property | Measurement | Unit |
---|---|---|
Specific surface area | aaaaa | aaaaa |
Specific surface area | aaaaa | aaaaa |
Specific surface area | aaaaa | aaaaa |
Abstract
Description
Claims
Application Information
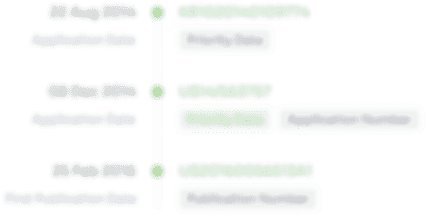
- R&D Engineer
- R&D Manager
- IP Professional
- Industry Leading Data Capabilities
- Powerful AI technology
- Patent DNA Extraction
Browse by: Latest US Patents, China's latest patents, Technical Efficacy Thesaurus, Application Domain, Technology Topic.
© 2024 PatSnap. All rights reserved.Legal|Privacy policy|Modern Slavery Act Transparency Statement|Sitemap