Fireproof door core plate and production method thereof
A technology of fire door core board and normal temperature, which is applied in the field of fire door core board and preparation, can solve the problems of great physical damage to production personnel, troublesome production process, and poor fire performance, so as to save production process, improve fire resistance and fire resistance, and enhance intensity effect
- Summary
- Abstract
- Description
- Claims
- Application Information
AI Technical Summary
Benefits of technology
Problems solved by technology
Method used
Examples
Embodiment 1
[0022] A fire door core board, comprising the following raw materials in mass fractions: 50 parts of deionized water, 30 parts of magnesium chloride, 5 parts of magnesium chloride, 0.5 parts of polyacrylonitrile-based carbon fiber, 0.5 part of polypropylene fiber, 10 parts of calcium bicarbonate, 1 part of modifier, 5 parts of silica fume, 10 parts of vegetable foaming agent, 5 parts of sodium carboxymethyl cellulose, 1 part of phosphoric acid. The polyacrylonitrile-based carbon fibers and polypropylene fibers have a length of 5 mm.
[0023] A method for preparing a fire door core board, comprising the following steps:
[0024] Step 1. Mix magnesium chloride and magnesium chloride with ionized water in turn, stir at room temperature for 10 minutes, and let stand to room temperature;
[0025] Step 2. Then add polyacrylonitrile-based carbon fiber and polypropylene fiber and stir at room temperature for 30 minutes, then keep warm at 30°C for 10 minutes, and then cool to room temper
Embodiment 2
[0032] A fire door core board, comprising the following raw materials in mass fractions: 60 parts of deionized water, 40 parts of magnesium chloride, 15 parts of magnesium chloride, 1 part of polyacrylonitrile-based carbon fiber, 1 part of polypropylene fiber, 15 parts of calcium bicarbonate, 2 parts of modifier, 10 parts of silica fume, 20 parts of vegetable foaming agent, 10 parts of sodium carboxymethyl cellulose, 2 parts of phosphoric acid. The polyacrylonitrile-based carbon fibers and polypropylene fibers have a length of 10 mm.
[0033] A method for preparing a fire door core board, comprising the following steps:
[0034] Step 1. Mix magnesium chloride and magnesium chloride with ionized water in turn, stir at room temperature for 15 minutes, and let stand to room temperature;
[0035] Step 2, add polyacrylonitrile-based carbon fiber and polypropylene fiber and stir at room temperature for 55 minutes, then keep warm at 32°C for 15 minutes, and then cool to room temperatur
Embodiment 3
[0042] A fire door core board, comprising the following raw materials in mass fractions: 55 parts of deionized water, 35 parts of magnesium chloride, 10 parts of magnesium chloride, 0.7 parts of polyacrylonitrile-based carbon fiber, 0.7 part of polypropylene fiber, 12 parts of calcium bicarbonate, 1.5 parts of modifier, 7 parts of silica fume, 15 parts of vegetable foaming agent, 7 parts of sodium carboxymethyl cellulose, 1.5 parts of phosphoric acid. The polyacrylonitrile-based carbon fibers and polypropylene fibers have a length of 7 mm.
[0043] A method for preparing a fire door core board, comprising the following steps:
[0044] Step 1. Mix magnesium chloride and magnesium chloride with ionized water in turn, stir at room temperature for 12 minutes, and let stand to room temperature;
[0045] Step 2. Then add polyacrylonitrile-based carbon fiber and polypropylene fiber and stir at room temperature for 40 minutes, then keep warm at 34°C for 12 minutes, and then cool to room
PUM
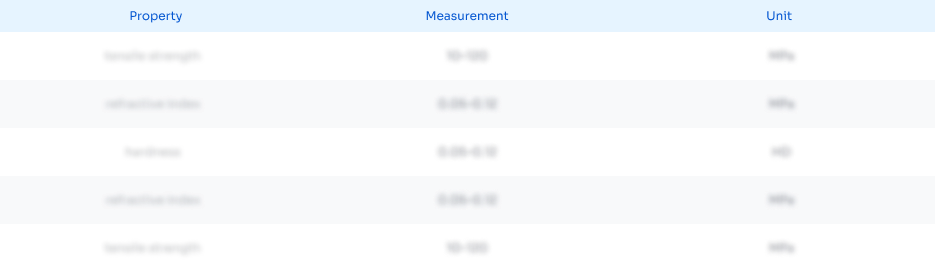
Abstract
Description
Claims
Application Information
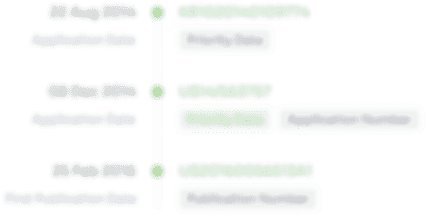
- R&D Engineer
- R&D Manager
- IP Professional
- Industry Leading Data Capabilities
- Powerful AI technology
- Patent DNA Extraction
Browse by: Latest US Patents, China's latest patents, Technical Efficacy Thesaurus, Application Domain, Technology Topic.
© 2024 PatSnap. All rights reserved.Legal|Privacy policy|Modern Slavery Act Transparency Statement|Sitemap