Copper fin-porous copper composite part, preparation method thereof and fin type copper composite radiator
A porous copper and fin technology, used in indirect heat exchangers, heat exchange equipment, lighting and heating equipment, etc., can solve the problem that porous metal or fins are insufficient in thermal conductivity enhancement, and the heat dissipation effect cannot be brought into full play. To achieve temperature control or heat dissipation and other issues, to achieve the effect of improving heat dissipation, low interface thermal resistance, and reducing manufacturing processes
- Summary
- Abstract
- Description
- Claims
- Application Information
AI Technical Summary
Problems solved by technology
Method used
Image
Examples
Example Embodiment
[0054] The present application proposes a method for preparing copper fin-porous copper composite parts, comprising the following steps:
[0055] Co-injection of the copper feed for preparing copper fins and the porous copper feed for preparing porous copper to obtain a green copper fin-porous copper composite structure; followed by degreasing and sintering to obtain a one-time formed copper fin Sheet-porous copper composite parts;
[0056] Among them, the shrinkage ratio of copper feed and porous copper feed is equal.
[0057] By using metal injection molding technology to form copper fins and porous copper into copper fin-porous copper composite parts at one time, the parts can be made with high dimensional accuracy and can be mass-produced, which not only reduces the manufacturing process, but also greatly reduces the cost. In addition, in the obtained copper fin-porous copper composite parts, the copper fin and the porous copper interface are metallurgically bonded, the inte
Example Embodiment
[0096] Example 1
[0097] This embodiment provides a finned copper composite heat sink with high thermal conductivity, which specifically includes:
[0098] Select the atomized copper powder with a particle size of less than 30μm and an average particle size of 8μm;
[0099] The organic binder with polyoxymethylene as the main component is selected, and the mass fraction of polyoxymethylene is 85%;
[0100] Select PA6 particles with an average particle size of 500 μm;
[0101] According to the volume fraction of 50% each, weigh the copper powder and PA6 particles for use;
[0102] Weigh the polyoxymethylene-based binder according to the shrinkage ratio of 1.16 for use;
[0103] The weighed atomized copper powder and the polyoxymethylene-based binder were mixed in an internal mixer at 190 °C for 0.5 h under the protection of an argon atmosphere, and then cooled to 170 °C, and then PA6 particles were added to continue the internal mixing for 1 h to obtain porous copper. feeding
Example Embodiment
[0109] Example 2
[0110] This embodiment provides a finned copper composite heat sink with high thermal conductivity, which specifically includes:
[0111] Select the atomized copper powder with a particle size of less than 30μm and an average particle size of 10μm;
[0112] The organic binder with polyoxymethylene as the main component is selected, and the mass fraction of polyoxymethylene is 85%;
[0113] Select PA6 particles with an average particle size of 100 μm;
[0114] Weigh the copper powder and PA6 particles according to the volume fraction of 20% and 80%, respectively;
[0115] Weigh the polyoxymethylene-based binder according to the shrinkage ratio of 1.16 for use;
[0116] The weighed atomized copper powder and the polyoxymethylene-based binder were mixed in an internal mixer at 190 °C for 0.5 h under the protection of an argon atmosphere, and then cooled to 170 °C, and then PA6 particles were added to continue the internal mixing for 1 h to obtain porous copper.
PUM
Property | Measurement | Unit |
---|---|---|
The average particle size | aaaaa | aaaaa |
Average pore size | aaaaa | aaaaa |
Thermal resistance | aaaaa | aaaaa |
Abstract
Description
Claims
Application Information
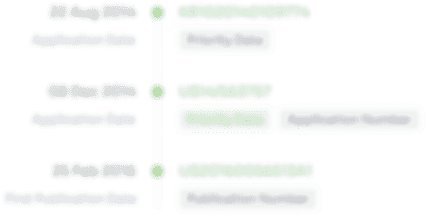
- R&D Engineer
- R&D Manager
- IP Professional
- Industry Leading Data Capabilities
- Powerful AI technology
- Patent DNA Extraction
Browse by: Latest US Patents, China's latest patents, Technical Efficacy Thesaurus, Application Domain, Technology Topic.
© 2024 PatSnap. All rights reserved.Legal|Privacy policy|Modern Slavery Act Transparency Statement|Sitemap