Heating method of preventing for high-carbon steel blank or steel ingot from decarbonizing
A heating method and billet technology, applied in heat treatment furnaces, heat treatment equipment, furnaces, etc., can solve problems such as waste of energy, slow heating of billets, and insufficient oxygen, and achieve the effects of increased labor intensity, short heating time, and increased costs
- Summary
- Abstract
- Description
- Claims
- Application Information
AI Technical Summary
Problems solved by technology
Method used
Examples
Example Embodiment
[0022] Example:
[0023] When producing T11A (carbon range 1.05~1.14%) φ6.5mm wire rod figure 1 process flow.
[0024] heating furnace
[0025] The specific description for the above table is as follows:
[0026] ①When the walking heating furnace heats a 110mm×110mm steel billet, in the three stages of preheating, heating period and holding period of the whole heating process, the strong oxidizing oxygen atmosphere of the method of the present invention is used for heating, and the air in the strong oxidizing atmosphere is excessive The coefficient (the ratio of air to gas) is controlled between 1.2 and 1.4.
[0027] ②When the 110mm×110mm billet is in the preheating period of the walking heating furnace, the temperature of the billet is about 700°C or less, the maximum furnace temperature in the preheating section is controlled between 1050 and 1100°C, and the excess air coefficient in the furnace is controlled at Between 1.2 and 1.4. At this time, the original oxid
PUM
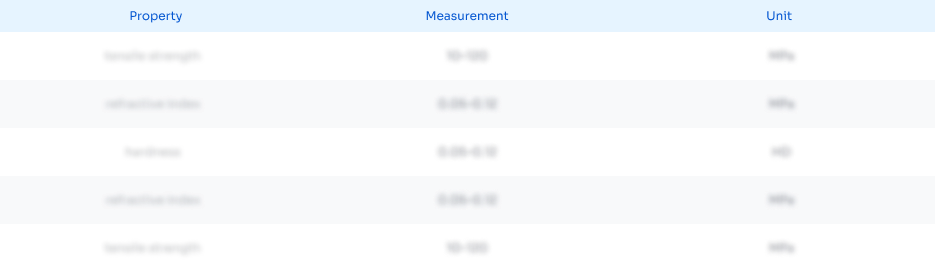
Abstract
Description
Claims
Application Information
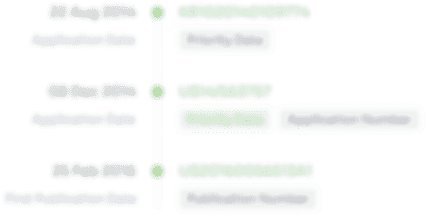
- R&D Engineer
- R&D Manager
- IP Professional
- Industry Leading Data Capabilities
- Powerful AI technology
- Patent DNA Extraction
Browse by: Latest US Patents, China's latest patents, Technical Efficacy Thesaurus, Application Domain, Technology Topic.
© 2024 PatSnap. All rights reserved.Legal|Privacy policy|Modern Slavery Act Transparency Statement|Sitemap