Method and its device for producing catalyst grade super high purity Sb2O3
An antimony trioxide and production method technology, applied in chemical instruments and methods, inorganic chemistry, antimony compounds and other directions, can solve the problems of easy melt-through of air supply pipes, product pollution, non-conformity, etc., and achieve stable and reliable product quality. The effect of reducing production cost and energy consumption
- Summary
- Abstract
- Description
- Claims
- Application Information
AI Technical Summary
Benefits of technology
Problems solved by technology
Method used
Image
Examples
Embodiment 1
[0021] Embodiment 1: Production device adopts figure 1 The antimony white furnace shown uses metal antimony as raw material, and its chemical composition is Sb 99.89%, Pb 0.05%, As 0.02%, Fe 0.011%. Put in the metal antimony to melt, and when the molten antimony liquid in the furnace reaches more than 2 tons, spray 0.1-0.8MPa compressed air on the surface of the antimony liquid to oxidize and volatilize the antimony; Compressed air flow and supplementary heating with heating elements 5 and 15 to increase the temperature of antimony trioxide flue gas to above 1200°C, and control the high temperature antimony trioxide when the flue gas leaves the high temperature reaction chamber 13 and enters the quenching mixer 9 The ratio of the total amount of flue gas to the amount of quenching air is 1:6, and 300kg of metal antimony is put into the furnace every hour, and the resulting products are collected by a bag dust collection system, and 340kg of antimony trioxide products are obtained
Embodiment 2
[0027] Embodiment 2: metal antimony chemical composition used is Sb 99.96%, Pb 0.005%, As 0.0048%, Fe 0.011%, all the other conditions are with embodiment 1, and the physical and chemical index detection result of its gained product is as follows:
[0028] Sb 2 o 3 99.94% As 0.0041%
[0029] Pb 0.0043% Fe 0.0010%
[0030] EG dissolved light transmittance 99.1% hydrochloric acid dissolved turbidity 3.9ppm
[0031] Whiteness 98.5% b value 0.90
[0032] Average particle size 0.58μm Cubic crystal form 99.3%
Embodiment 3
[0033] Embodiment 3: Production device adopts figure 2 The antimony white furnace shown uses metal antimony as raw material, and its chemical composition is Sb 99.90%, As 0.03%, Pb 0.04%, Fe 0.014%. The antimony is melted, and when the molten antimony liquid in the furnace reaches more than 2 tons, spray 0.1-0.8 MPa compressed air on the surface of the antimony liquid to oxidize and volatilize the antimony, and stop the heating of the fire chamber 21 at the same time. Enter the compressed air flow on the surface of the antimony liquid to increase the reaction temperature in the furnace to above 1100°C. Use liquefied petroleum gas or other fuels to maintain the temperature in the gasification reaction chamber 17 at 1300-1500°C. When the room 17 enters the quenching mixer 9, the ratio of the total amount of high-temperature antimony trioxide flue gas to the total amount of quenching air is controlled to be 1:8, and 350 kg of metal antimony is put into the furnace every hour, and t
PUM
Property | Measurement | Unit |
---|---|---|
Turbidity | aaaaa | aaaaa |
Turbidity | aaaaa | aaaaa |
Turbidity | aaaaa | aaaaa |
Abstract
Description
Claims
Application Information
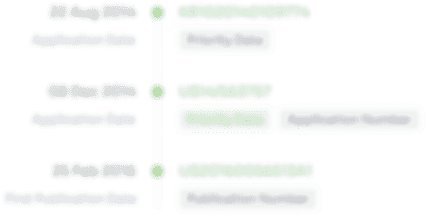
- R&D Engineer
- R&D Manager
- IP Professional
- Industry Leading Data Capabilities
- Powerful AI technology
- Patent DNA Extraction
Browse by: Latest US Patents, China's latest patents, Technical Efficacy Thesaurus, Application Domain, Technology Topic.
© 2024 PatSnap. All rights reserved.Legal|Privacy policy|Modern Slavery Act Transparency Statement|Sitemap