Method of manufacturing plasma display device
一种显示装置、等离子体的技术,应用在辨认装置、仪器等方向,能够解决分离作业耗时、繁琐等问题
- Summary
- Abstract
- Description
- Claims
- Application Information
AI Technical Summary
Problems solved by technology
Method used
Examples
no. 1 approach
[0029] Next, a method of manufacturing the plasma display device according to the first embodiment will be described with reference to FIGS. 1 to 8 . However, embodiments of the present invention are not limited thereto.
[0030] FIG. 1 shows the configuration of a screen of a plasma display device according to a first embodiment of the present invention. As shown in FIG. 1 , on a transparent front-side substrate 1 such as a glass substrate, a plurality of rows of stripe-shaped display electrodes 2 are formed, in which scan electrodes and sustain electrodes form a pair. Furthermore, a dielectric layer 3 is formed to cover the electrode group, and a protective film 4 is formed on the dielectric layer 3 .
[0031] In addition, on the back side substrate 5 disposed opposite to the front side substrate 1 , a plurality of rows of strip-shaped data electrodes 7 covered by the coating layer 6 are formed so as to intersect with the display electrodes 2 of the scan electrodes and the ...
no. 2 approach
[0056] Next, a second embodiment of the present invention will be described. 9 is a cross-sectional view in a direction perpendicular to adhesive material 17 of the plasma display device according to the second embodiment. FIG. 10 is a plan view showing the application shape of the adhesive material 17 .
[0057] As shown in Fig. 9 and Fig. 10, for the adhesive material 17, the width on the side of the peeling start point 17A is wider, and the width gradually becomes narrower from the peeling start point 17A to the peeling end point 17B. Instead, it is coated and arranged between the screen 10 and the bottom plate member 14 . In addition, the rectangular adhesive materials 17 are arranged so that the peeling start points 17A of the adhesive materials 17 are alternately located on opposite sides of the bottom plate member 14 . That is, as shown in FIG. 10 , the rectangular adhesive materials 17 are arranged such that the intervals between them are substantially constant and u...
no. 3 approach
[0064] Next, a third embodiment of the present invention will be described. 12 is a cross-sectional view in a direction perpendicular to adhesive material 17 of the plasma display device according to the third embodiment. FIG. 13 is a plan view showing the application shape of the adhesive material 17 .
[0065] As shown in FIGS. 12 and 13 , the adhesive materials 17 are arranged in a plurality of rows at predetermined intervals between the screen 10 and the bottom plate member 14 . Furthermore, a plurality of spacers 21 for defining a gap between the screen 10 and the bottom plate member 14 are arranged between the plurality of rectangular adhesive materials 17 . The spacer 21 is configured by arranging a stretch-peelable adhesive 21A in an island shape, and embedding beads 21B such as glass beads or resin beads in the island-shaped adhesive 21A.
[0066] In addition, the rectangular adhesive material 17 is desirably arranged so that a part of it protrudes from between the ...
PUM
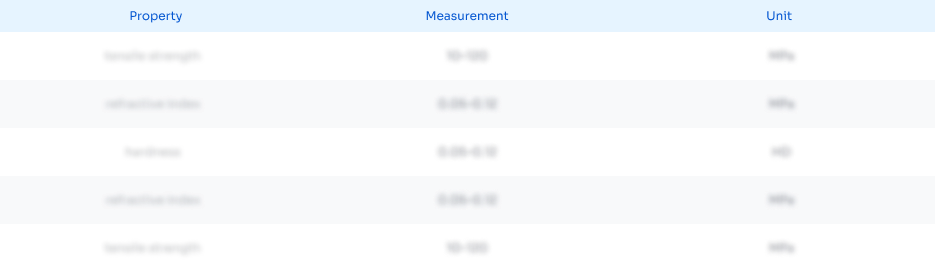
Abstract
Description
Claims
Application Information
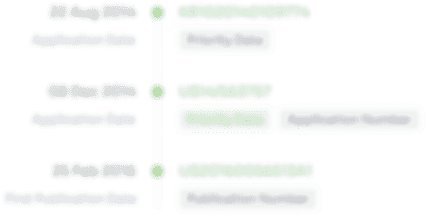
- R&D Engineer
- R&D Manager
- IP Professional
- Industry Leading Data Capabilities
- Powerful AI technology
- Patent DNA Extraction
Browse by: Latest US Patents, China's latest patents, Technical Efficacy Thesaurus, Application Domain, Technology Topic.
© 2024 PatSnap. All rights reserved.Legal|Privacy policy|Modern Slavery Act Transparency Statement|Sitemap