Medium density board produced with paper-making sludge and producing method thereof
A papermaking sludge, medium density technology, applied in papermaking, textile and papermaking, fiberboard, etc., can solve the problems of high processing cost, waste of land resources, secondary pollution, etc., and achieve low production cost, heat saving, and land resources. Effect
- Summary
- Abstract
- Description
- Claims
- Application Information
AI Technical Summary
Problems solved by technology
Method used
Examples
Example Embodiment
[0012] Example 1
[0013] In the present invention, papermaking sludge is used as raw material, which is mechanically dehydrated, formed and compounded into a wet medium density board with a moisture content of 70%, and then the wet medium density board is put into a press dryer and passed through Further dehydration, high-pressure setting under the pressure of 0.4MPa, and high-temperature drying at 170°C for 30 minutes to make finished MDF products. According to needs, the thickness of the finished MDF can be made into 1.2mm~3mm.
Example Embodiment
[0014] Example 2
[0015] In the present invention, papermaking sludge is used as raw material, and plant fibers accounting for 2% of the dry weight of papermaking sludge are added to the raw material of papermaking sludge for conditioning to enhance the mechanical properties of medium density boards, and then undergo mechanical dehydration, molding and Composite into wet medium density board with a moisture content of 70%, then put the wet medium density board into the press dryer, further dehydration in the press dryer, high pressure setting under the pressure of 0.4MPa, at 170 ℃ Dry at a high temperature for 30 minutes at a certain temperature to make a finished MDF product.
Example Embodiment
[0016] Example 3
[0017] The present invention takes papermaking sludge as raw material, and firstly adds plant fibers accounting for 2% of the absolute dry weight of the papermaking sludge to the raw material of the papermaking sludge for conditioning to enhance the mechanical properties of the medium density board. Starch with a dry weight of 1‰ and aluminum sulfate accounting for 3‰ of the absolute dry weight of the paper sludge to enhance the dehydration performance of the paper sludge. The purpose of adding aluminum sulfate is to adjust the pH value and dehydration performance of the sludge. The pH value is adjusted to 6-9, which is beneficial to environmental protection. Then, it is mechanically dehydrated, shaped and composited into a wet medium density board with a moisture content of 70%, and then the wet medium density board is put into a squeeze dryer, which is further dehydrated in the squeeze dryer, and is heated at 0.4MPa High-pressure shaping under pressure, high
PUM
Property | Measurement | Unit |
---|---|---|
Thickness | aaaaa | aaaaa |
Abstract
Description
Claims
Application Information
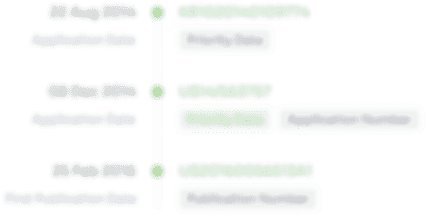
- R&D Engineer
- R&D Manager
- IP Professional
- Industry Leading Data Capabilities
- Powerful AI technology
- Patent DNA Extraction
Browse by: Latest US Patents, China's latest patents, Technical Efficacy Thesaurus, Application Domain, Technology Topic.
© 2024 PatSnap. All rights reserved.Legal|Privacy policy|Modern Slavery Act Transparency Statement|Sitemap