Pallet with strength plates and related methods
a technology of strength plates and pallets, applied in the field of pallets, can solve the problems of shortening the lifespan of the pallet, affecting the resilience of the pallet, and the end deck board may not be able to withstand such an impact, so as to improve the resilience to impacts and increase the cost
- Summary
- Abstract
- Description
- Claims
- Application Information
AI Technical Summary
Benefits of technology
Problems solved by technology
Method used
Examples
Embodiment Construction
[0028] The present invention will now be described more fully hereinafter with reference to the accompanying drawings, in which preferred embodiments of the invention are shown. This invention may, however, be embodied in many different forms and should not be construed as limited to the embodiments set forth herein. Rather, these embodiments are provided so that this disclosure will be thorough and complete, and will fully convey the scope of the invention to those skilled in the art. Like numbers refer to like elements throughout, and prime and double prime notations are used to indicate similar elements in alternative embodiments.
[0029] Referring initially to FIGS. 1-4, the pallet 10 in accordance with the invention comprises a base layer 20, a cargo layer 30 and a plurality of “stepped” support blocks 40. The support blocks 40 are coupled between the base and cargo layers 20, 30 and define a space 50 therebetween for receiving at least one lifting member of material handling eq...
PUM
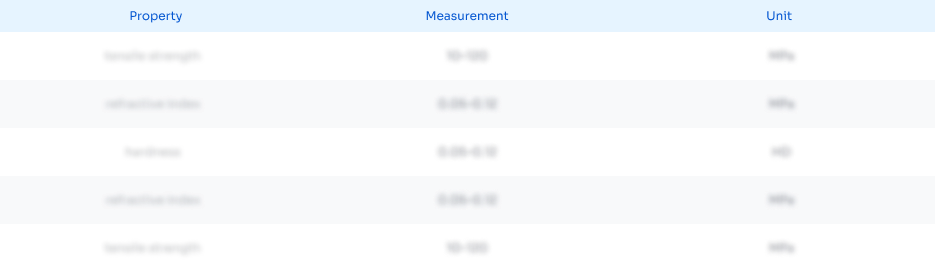
Abstract
Description
Claims
Application Information
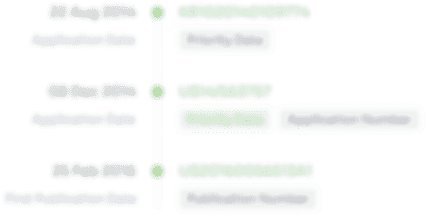
- R&D Engineer
- R&D Manager
- IP Professional
- Industry Leading Data Capabilities
- Powerful AI technology
- Patent DNA Extraction
Browse by: Latest US Patents, China's latest patents, Technical Efficacy Thesaurus, Application Domain, Technology Topic.
© 2024 PatSnap. All rights reserved.Legal|Privacy policy|Modern Slavery Act Transparency Statement|Sitemap