Zirconium Oxide Powder, Process For Producing The Same, And Material For Thermal Spraying
a technology thermal spraying, which is applied in the direction of natural mineral layered products, cellulosic plastic layered products, transportation and packaging, etc., can solve problems such as complicated operation, and achieve the effect of easy production of zirconium oxide powder
- Summary
- Abstract
- Description
- Claims
- Application Information
AI Technical Summary
Benefits of technology
Problems solved by technology
Method used
Image
Examples
example 1
[0041]As hydrated zirconia, an uncalcined material of KZ-0Y manufactured by KCM Corporation was used. Hydrated zirconia had a BET specific surface area of 175 m2 / g, a LOI of 12.3% and a crystal structure which was the same type as monoclinic zirconium oxide crystal, and a peak profile broader than the peak profile of monoclinic zirconium oxide crystal in an X-ray diffraction pattern (FIG. 1). One kg of the hydrated zirconia was charged into a quartz vessel, and placed in a quartz furnace together with the vessel. A hydrogen chloride gas (manufactured by Tsurumi Soda Co., Ltd., cylinder hydrogen chloride gas, purity 99.9%) was introduced into the furnace tube under the following conditions for 30 minutes.
flow rate: about 5 cm / minutes
temperature: 25° C. (room temperature)
The temperature was elevated at 300° C. / hour and kept at 1100° C. for 30 minutes while introducing a hydrogen chloride gas. Thereafter, a hydrogen chloride gas was replaced by a nitrogen gas, and the temperature wa
example 2
[0042]The powder 1 was charged in a dry ball mill [media: nylon coated iron balls (trade name: HighPla ball)], and deagglomerated for 2 hours to obtain a powder 2. The scanning electron micrograph of the powder 2 was shown in FIG. 3. The powder 2 had the same particle shape, D50 and D90 / D10 as those of the powder 1.
PUM
Property | Measurement | Unit |
---|---|---|
Fraction | aaaaa | aaaaa |
Fraction | aaaaa | aaaaa |
Fraction | aaaaa | aaaaa |
Abstract
Description
Claims
Application Information
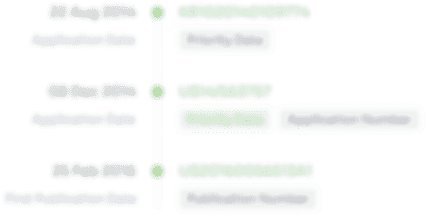
- R&D Engineer
- R&D Manager
- IP Professional
- Industry Leading Data Capabilities
- Powerful AI technology
- Patent DNA Extraction
Browse by: Latest US Patents, China's latest patents, Technical Efficacy Thesaurus, Application Domain, Technology Topic.
© 2024 PatSnap. All rights reserved.Legal|Privacy policy|Modern Slavery Act Transparency Statement|Sitemap