Production method of high-concentration sulfur dioxide gas
A sulfur dioxide and production method technology, applied in chemical instruments and methods, inorganic chemistry, sulfur compounds, etc., can solve the problems of waste heat waste, inconvenient use of safe transportation, large cooling water consumption, etc., and achieve the effect of avoiding overheating
- Summary
- Abstract
- Description
- Claims
- Application Information
AI Technical Summary
Problems solved by technology
Method used
Image
Examples
Embodiment 1
[0013] Embodiment 1 of the present invention: a kind of production method of high-concentration sulfur dioxide gas, as attached figure 1 As shown, after the high-temperature sulfur dioxide flue gas produced by the combustion of the sulfur incinerator is cooled, part of the flue gas passes through the flue gas fan, returns to the front end of the entire production system through the pipeline, mixes with air, and enters the sulfur incinerator together. The concentration of sulfur dioxide gas in the mixed gas is less than or equal to 5.36%, and the remaining flue gas of sulfur dioxide enters the downstream process. At the same time, the liquid sulfur is sent to the sulfur furnace for spray combustion under the action of the liquid sulfur pump, and the flue gas of sulfur dioxide is discharged. And so on and on.
[0014] The high-temperature sulfur dioxide flue gas produced by the combustion of the sulfur incinerator is first cooled to 310°C-330°C by the waste heat boiler, and then...
PUM
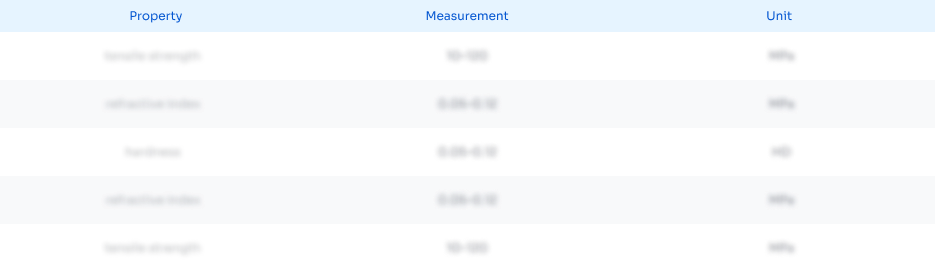
Abstract
Description
Claims
Application Information
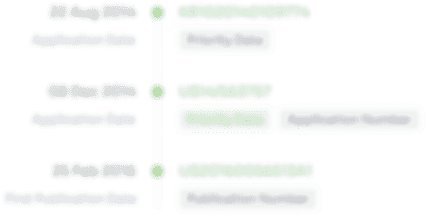
- R&D Engineer
- R&D Manager
- IP Professional
- Industry Leading Data Capabilities
- Powerful AI technology
- Patent DNA Extraction
Browse by: Latest US Patents, China's latest patents, Technical Efficacy Thesaurus, Application Domain, Technology Topic.
© 2024 PatSnap. All rights reserved.Legal|Privacy policy|Modern Slavery Act Transparency Statement|Sitemap