Mesostructured aluminosilicate material made of spherical particles of specific size
- Summary
- Abstract
- Description
- Claims
- Application Information
AI Technical Summary
Benefits of technology
Problems solved by technology
Method used
Examples
example 1 (
Invention)
Preparation of an Aluminosilicate Material of Si / Al Ratio=4 According to the Main Preparation Method of the Invention
[0038]1 kg hexahydrated aluminium trichloride is added to a solution containing 10 kg ethanol, 5 l water, 36 ml HCl and 1.4 kg surfactant CTAB. The assembly is left under stirring at ambient temperature until complete dissolution of the aluminic precursor. 3.6 kg tetraethylorthosilicate (TEOS) are then added. After 10-min stirring at ambient temperature, the assembly is atomized by means of a “mono-fluid” spray nozzle in a chamber into which a carrier gas, a dry air / nitrogen mixture, is sent. The droplets obtained by atomization are dried between 100° C. and 120° C. according to the protocol described in the above description of the invention, in accordance with stage c) of the main method of the invention. The particles are collected in a bag filter. Said particles are crushed by means of a jet mill and brought down to some pm (3 to 5 μm). A 30 wt. % fract
example 3 (
Invention)
Preparation of an Aluminosilicate Material of Si / Al Ratio=9 According to the Simplified Preparation Method of the Invention
[0040]520 g hexahydrated aluminium trichloride are added to a solution containing 10 kg ethanol, 5 l water, 36 ml HCl and 1.4 kg surfactant P123. The assembly is left under stirring at ambient temperature until complete dissolution of the aluminic precursor. 4.0 kg tetraethylorthosilicate (TEOS) are then added. After 18-hour stirring at ambient temperature, the assembly is atomized by means of a “mono-fluid” spray nozzle in a chamber into which a carrier gas, a dry air / nitrogen mixture, is sent. The droplets obtained by atomization are dried between 100° C. and 120° C. according to the protocol described in the above description of the invention, in accordance with stage c) of the simplified method of the invention. The particles are collected in a bag filter in form of a powder that is then calcined in air for 5 hours at T=550° C. in order to remove
PUM
Property | Measurement | Unit |
---|---|---|
Fraction | aaaaa | aaaaa |
Pore size | aaaaa | aaaaa |
Pore size | aaaaa | aaaaa |
Abstract
Description
Claims
Application Information
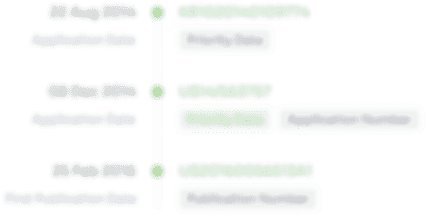
- R&D Engineer
- R&D Manager
- IP Professional
- Industry Leading Data Capabilities
- Powerful AI technology
- Patent DNA Extraction
Browse by: Latest US Patents, China's latest patents, Technical Efficacy Thesaurus, Application Domain, Technology Topic.
© 2024 PatSnap. All rights reserved.Legal|Privacy policy|Modern Slavery Act Transparency Statement|Sitemap