Release Agent for Toner, and Toner
- Summary
- Abstract
- Description
- Claims
- Application Information
AI Technical Summary
Benefits of technology
Problems solved by technology
Method used
Examples
Example
Example 1
[0070]In a 1 liter four necked flask equipped with a Dimroth condenser, a thermometer, a nitrogen inlet tube, and a stirrer, 120 g of α-olefin polymer A1 was placed to be melt by raising the temperature to 190° C. with the introduction of nitrogen. After 40 g of styrene and 2 g of dicumylperoxide were added during the space of time of 1 hour, the reaction mixture was retained at 190° C. for 1 hour. A following vacuum distillation with the pressure of 7 hPa at 190° C. for 1 hour provided the release agent for toner R1. R1 had 85 mass % of 2-butanone insoluble component, the melting point (Tm) of 52° C., which was represented by a single DSC peak having the half-height width of 8.3° C., and the weight average molecular weight (Mw) of 43,000.
Example
Example 2
[0071]The release agent for toner R2 was provided in the same method as example 1 except that the α-olefin polymer A2 was used instead of A1.
[0072]R2 had 87 mass % of 2-butanone insoluble component, the melting point (Tm) of 70° C., which was represented by a single DSC peak having the half-height width of 6.0° C., and the weight average molecular weight (Mw) of 9,000.
Example
Example 3
[0073]In a 1 liter four necked flask equipped with a Dimroth condenser, a thermometer, a nitrogen inlet tube, and a stirrer, 120 g of α-olefin polymer A2 was placed to be melt by raising the temperature to 160° C. with the introduction of nitrogen. After 80 g of styrene and 4 g of dicumylperoxide were added during the space of time of 1 hour, the reaction mixture was retained at 160° C. for 1 hour. A following vacuum distillation with the pressure of 7 hPa at 190° C. for 1 hour provided the release agent for toner R3. R3 had 74 mass % of 2-butanone insoluble component, the melting point (Tm) of 67° C., which was represented by a single DSC peak having the half-height width of 6.0° C., and the weight average molecular weight (Mw) of 20,000.
PUM
Property | Measurement | Unit |
---|---|---|
Temperature | aaaaa | aaaaa |
Temperature | aaaaa | aaaaa |
Temperature | aaaaa | aaaaa |
Abstract
Description
Claims
Application Information
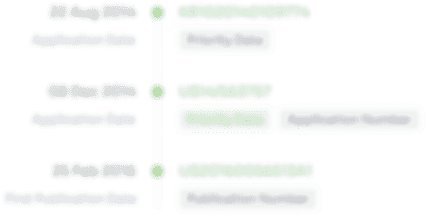
- R&D Engineer
- R&D Manager
- IP Professional
- Industry Leading Data Capabilities
- Powerful AI technology
- Patent DNA Extraction
Browse by: Latest US Patents, China's latest patents, Technical Efficacy Thesaurus, Application Domain, Technology Topic.
© 2024 PatSnap. All rights reserved.Legal|Privacy policy|Modern Slavery Act Transparency Statement|Sitemap