Methods For Reducing Ferrous Corrosion
- Summary
- Abstract
- Description
- Claims
- Application Information
AI Technical Summary
Problems solved by technology
Method used
Image
Examples
example 1
on of Anti-Rust Additives
[0087]The following anti-rust additives were prepared using standard methods:
example 2
Anti-Rust Additive on Rust Formation
[0088]The effect of an anti-rust additive from Example 1 (OX6) on the rust-preventing characteristics of two different base fuels for a spark-ignition internal combustion engine was measured.
[0089]The anti-rust additive was added to the fuels at a treat rate of 1.34% weight additive / weight base fuel, equivalent to a treat rate of 10 g additive / fuel. The first fuel was an E0 gasoline base fuel. The second fuel was an E10 gasoline base fuel.
[0090]The rust-preventing characteristics of the base fuels, as well as the blends of base fuel and anti-rust additive, were determined according to a modified version of ASTM D 665, in which the test was carried out at 23° C., rather than 60° C. Accordingly, a mixture of 300 mL of the fuel being tested was stirred for 24 h with 30 mL of distilled water at 23° C. A cylindrical steel test rod was completely immersed therein. The presence and degree of rusting (expressed as a percentage of rod surface on which rus
example 3
mber of Fuels Containing Anti-Rust Additives
[0093]The effect of anti-rust additives from Example 1 (OX1, OX2, OX3, OX5, OX6, OX8, OX9, OX12, OX13, OX17 and OX19) on the octane number of two different base fuels for a spark-ignition internal combustion engine was measured.
[0094]The additives were added to the fuels at a relatively low treat rate of 0.67% weight additive / weight base fuel, equivalent to a treat rate of 5 g additive / litre of fuel. The first fuel was an E0 gasoline base fuel. The second fuel was an E10 gasoline base fuel. The RON and MON of the base fuels, as well as the blends of base fuel and anti-rust additive, were determined according to ASTM D2699 and ASTM D2700, respectively.
[0095]The following table shows the RON and MON of the fuel and the blends of fuel and anti-rust additive, as well as the change in the RON and MON that was brought about by using the anti-rust additives:
E0 base fuelE10 base fuelAdditiveRONMONΔRONΔMONRONMONΔRONΔMON—95.486.0n / an / a95.485.2n
PUM
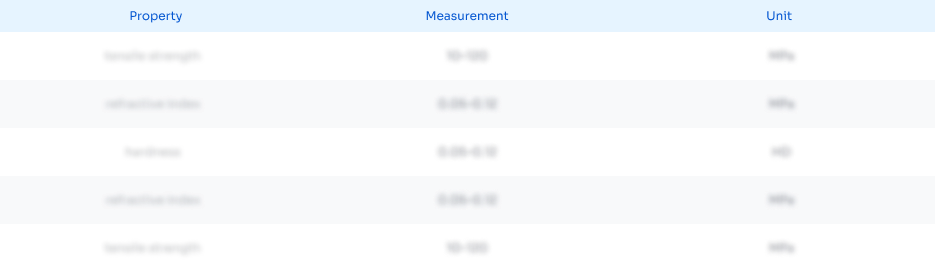
Abstract
Description
Claims
Application Information
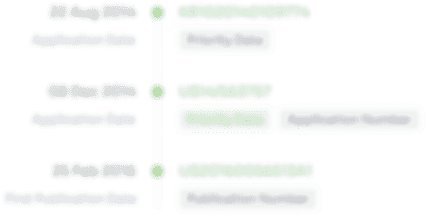
- R&D Engineer
- R&D Manager
- IP Professional
- Industry Leading Data Capabilities
- Powerful AI technology
- Patent DNA Extraction
Browse by: Latest US Patents, China's latest patents, Technical Efficacy Thesaurus, Application Domain, Technology Topic.
© 2024 PatSnap. All rights reserved.Legal|Privacy policy|Modern Slavery Act Transparency Statement|Sitemap