4d printing method for in-situ regulation of functional properties of nickel-titanium alloy and use thereof
a nickel-titanium alloy and functional property technology, applied in the field of additive manufacturing technology, can solve the problems of reducing the processing and production efficiency of nickel-titanium alloy parts, reducing the precision reducing the application of niti alloy parts, so as to achieve the effect of rapid manufacturing of niti alloy parts and expanding the application of niti alloys
- Summary
- Abstract
- Description
- Claims
- Application Information
AI Technical Summary
Benefits of technology
Problems solved by technology
Method used
Image
Examples
example 1
[0026]1. Atomization milling: Mixing Ti and Ni according to the atomic ratio of Ti 50.6 at. % and Ni 49.4 at. %, and smelting them in vacuum to obtain NiTi alloy bars; atomizing the bars to obtain the original powder, and sieving the original powder to control the particle size of the target powder in the range of 15-53 μm.
[0027]2. Powder modification: Using a Plasma-BM-S plasma ball mill to treat the sieved NiTi alloy powder (mass ml) by discharging with the following control parameters: the voltage at 130 V, the current at 1.4 A, the electrode speed at 800 r / min, the discharge plasma treatments for 6 times, each discharge treatment for 0.5 h, and an interval of 30 min between two adjacent discharge treatments; then adding Ni powder with a mass of m2 and a particle size of 100 nm to the NiTi alloy powder treated by the discharge plasma, and controlling the ratio of m1:m2 to 30:1, so that the ratio of Ti:Ni in the mixed powder was 49.1:50.9 (at. %); then adjusting the electrode speed
example 2
[0032]1. Milling: Mixing Ti and Ni according to the atomic ratio of Ti 60 at. % and Ni 40 at. %, and smelting them in vacuum to obtain NiTi alloy bars; atomizing the bars to obtain the original powder, and sieving the original powder to control the particle size of the target powder in the range of 15-53 μm.
[0033]2. Powder modification: Using a Plasma-BM-S plasma ball mill to treat the sieved NiTi alloy powder (mass m1) by discharging with the following control parameters: the voltage at 120 V, the current at 1 A, the electrode speed at 1000 r / min, the discharge treatments for 3 times, each discharge treatment for 1 h, and an interval of 45 min between two adjacent discharge treatments; then adding Ni powder with a mass of m2 and a particle size of 500 nm to the original powder after the discharge treatment, and controlling the ratio of m1:m2 to 4.91:1, so that the ratio of Ti:Ni in the mixed powder was 49.2:50.8 (at. %); then adjusting the electrode speed to 700 r / min and controll
example 3
[0036]1. Milling: Mixing Ti and Ni according to the atomic ratio of Ti 50 at. % and Ni 50 at. %, and smelting them in vacuum to obtain NiTi alloy bars; atomizing the bars to obtain the original powder, and sieving the original powder to control the particle size of the target powder in the range of 15-53 μm.
[0037]2. Powder modification: Using a Plasma-BM-S plasma ball mill to treat the sieved NiTi alloy powder (mass ml) by discharging with the following control parameters: the voltage at 125 V, the current at 1.4 A, the electrode speed at 800 r / min, the discharge treatments for 3 times, each discharge treatment for 1.5 h, and an interval of 30 min between two adjacent discharge treatments; then adding Ni powder with a mass of m2 and a particle size of 300 nm to the original powder after the discharge treatment, and controlling the ratio of m1:m2 to 44.4:1, so that the ratio of Ti:Ni in the mixed powder was 49:51 (at. %); then adjusting the electrode speed to 500 r / min and controlli
PUM
Property | Measurement | Unit |
---|---|---|
Length | aaaaa | aaaaa |
Current | aaaaa | aaaaa |
Current | aaaaa | aaaaa |
Abstract
Description
Claims
Application Information
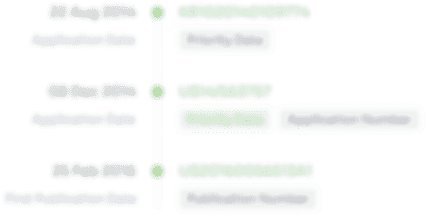
- R&D Engineer
- R&D Manager
- IP Professional
- Industry Leading Data Capabilities
- Powerful AI technology
- Patent DNA Extraction
Browse by: Latest US Patents, China's latest patents, Technical Efficacy Thesaurus, Application Domain, Technology Topic.
© 2024 PatSnap. All rights reserved.Legal|Privacy policy|Modern Slavery Act Transparency Statement|Sitemap