Method of making granules and the granulator
a technology of granules and granules, which is applied in the direction of granulation in rotating dishes/pans, presses, manufacturing tools, etc., can solve the problems of difficult to obtain accurately metered amounts of finely divided materials into a tablet die, granules that have low compactness and redisperse easily, and the rate limiting step in the production process has been found to be the extrusion stag
- Summary
- Abstract
- Description
- Claims
- Application Information
AI Technical Summary
Problems solved by technology
Method used
Examples
example 2
This is a comparative example that illustrates extrusions using a commercial granulator.
5 kg of a wet simazine mix identical to that described in Example 1 was prepared and passed through a No. 7 Jackson Crockatt granulator but in its unmodified configuration. It was fitted with the same 910 .mu.m aperture mesh and base plate used for Example 1 but the standard 3 blade Jackson Crockatt rotor replaced the rollers used in the granulator of Example 1. The extent and speed of reciprocation were the same as that of Example 1.
The wet mix was extruded satisfactorily and was converted to granules in accordance with the method described in Example 1. 95.4% of the dry granules by weight were in the size range of 0.5-1.7 mm. The extrusion rate was 54 kg / Hr and the rate per 1000 mm.sup.2 of exposed mesh was 3.3 kg / Hr which is significantly less than the rate in Example 1.
example 3
This Example illustrates the granulation of sodium lauryl sulfate detergent using a laboratory scale model of a granulator according to the invention.
A laboratory granulator was manufactured to be similar to the unit described in Example 1. It was made from stainless steel and consisted of a vertical cylindrical hopper of 75 mm internal diameter with 3 steel rollers, each 37 mm in diameter with a 12 mm wide smooth surface. The rollers were positioned an equal distance apart on steel support rods fixed at right angles to a reciprocating vertical shaft.
Granular sodium lauryl sulfate (Zoharpon SLS brand) was used.
A dry sieve analysis was carried out on the material as received, results as follows:
The detergent was first dry granulated adding it to the laboratory granulator fitted with a 910 .mu.m aperture woven stainless steel wire mesh tensioned over a perforated base plate. The roller assembly was adjusted so that the rollers were lightly tensioned on the mesh. The drive shaft recipr...
example 4
This Example illustrates the wet granulation of a commercial laundry detergent composition.
"Cold Power" distributed by Colgate-Palmolive Pty Ltd, was used.
A dry sieve analysis was carried out on a sample of "Cold Power" powder with the following results:
A wet mix was prepared by blending 200 g of "Cold Power" with 5 g of water. This was passed through the laboratory granulator described in Example 3. This was set up and operated in the same manner as described under Example 3. The wet mix extruded satisfactorily to produce cohesive extrudates, generally 2-4 mm in length. More energy was required to extrude the "Cold Power" pre-mix than the sodium lauryl sulfate pre-mix of Example 3.
The wet extrudates were rolled / tumbled vigorously for 120 seconds by hand in an inflated polyethylene bag which reduced them to reasonably smooth elongated granules. After drying at 45.degree. C., 95.7% of the granules by weight were in the size range of 0.5-1.7 mm.
PUM
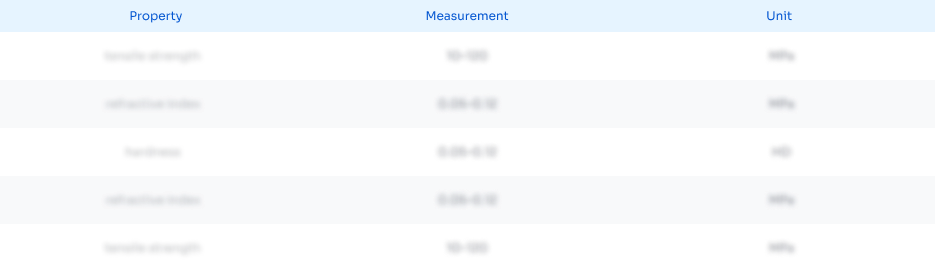
Abstract
Description
Claims
Application Information
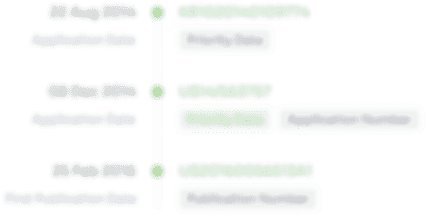
- R&D Engineer
- R&D Manager
- IP Professional
- Industry Leading Data Capabilities
- Powerful AI technology
- Patent DNA Extraction
Browse by: Latest US Patents, China's latest patents, Technical Efficacy Thesaurus, Application Domain, Technology Topic.
© 2024 PatSnap. All rights reserved.Legal|Privacy policy|Modern Slavery Act Transparency Statement|Sitemap