Printing plate material and image formation method employing the same
- Summary
- Abstract
- Description
- Claims
- Application Information
AI Technical Summary
Benefits of technology
Problems solved by technology
Method used
Image
Examples
example 1
(Preparation of Printing Plate Material)
[0159]The above-obtained coating solution was coated on the substrate obtained above employing a wire bar to obtain a combination as shown in Table 4, and dried to give an image formation layer having a dry thickness as shown in Table 4. Thus, inventive and comparative printing plate material samples were prepared.
[0160]The coated hydrophilic layer was dried at 80° C. for 3 minutes, and then further aged at 60° C. for 24 hours. The coated image formation layer was dried at 55° C. for 3 minutes, and then further aged at 55° C. for 24 hours.
(Image Formation)
[0161]Image formation was carried out by infrared laser exposure. Exposure was carried out employing an infrared laser (having a wavelength of 830 nm and a beam spot diameter of 18 μm) at an exposure energy of 300 mJ / cm2, at a resolution of 2400 dpi and at a screen line number of 175 to form an image, the beam being focused on the surface of the image formation layer. The term, “dpi” shows the
example 2
(Preparation of Printing Plate Material)
[0190]The above-obtained coating solution was coated on the substrate obtained above employing a wire bar to obtain a combination as shown in Table 5, and dried to give an image formation layer having a dry thickness as shown in Table 4. Thus, inventive and comparative printing plate material samples were prepared.
[0191]The coated hydrophilic layer was dried at 80° C. for 3 minutes, and then further aged at 60° C. for 24 hours. The coated image formation layer was dried at 55° C. for 3 minutes, and then further aged at 55° C. for 24 hours.
(Image Formation)
[0192]Image formation was carried out by infrared laser exposure. Exposure was carried out employing an infrared laser (having a wavelength of 830 nm and a beam spot diameter of 18 μm) at an exposure energy of 400 mJ / cm2, at a resolution of 2400 dpi and at a screen line number of 175 to form an image, the beam being focused on the surface of the image formation layer. A solid image and an imag
PUM
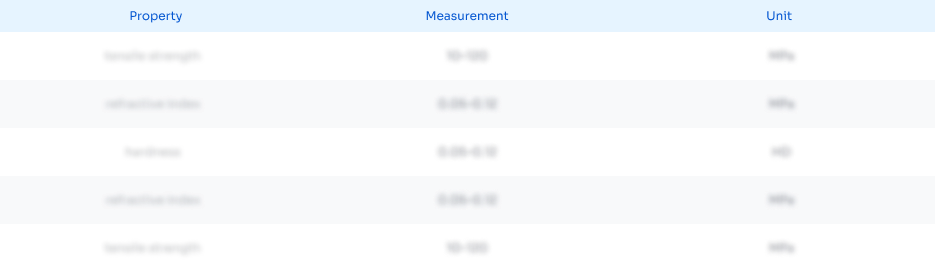
Abstract
Description
Claims
Application Information
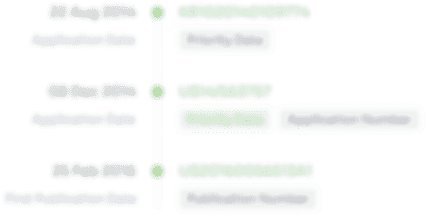
- R&D Engineer
- R&D Manager
- IP Professional
- Industry Leading Data Capabilities
- Powerful AI technology
- Patent DNA Extraction
Browse by: Latest US Patents, China's latest patents, Technical Efficacy Thesaurus, Application Domain, Technology Topic.
© 2024 PatSnap. All rights reserved.Legal|Privacy policy|Modern Slavery Act Transparency Statement|Sitemap