Method for producing high-temperature alloy by induction heating vacuum refining
A technology of induction heating and high-temperature alloys, which is applied in the field of high-temperature alloys, can solve the problems of poor product quality, high cost of raw materials, and poor ability to remove inclusions, and achieve the effects of reduced gas content in finished products, reduced inclusions in molten steel, and reduced production costs
- Summary
- Abstract
- Description
- Claims
- Application Information
AI Technical Summary
Benefits of technology
Problems solved by technology
Method used
Examples
Embodiment 1
[0028] Production of GH2132 superalloy
[0029] Use induction heating to melt the GH2132 molten steel matched in proportion in a 2-ton induction steelmaking furnace;
[0030] Raise the temperature of molten steel to 1450°C;
[0031] Adding CaO-Al on the surface of molten steel 2 o 3 Refining slag is 30kg; of which: CaO-Al 2 o 3 Medium is 10% Al 2 o 3 ;
[0032] After melting the refining slag, add a vacuum cover for vacuum treatment; during this process: on the one hand, argon gas is supplied to the furnace from the vent plug at the bottom of the refining ladle, and the flow rate of argon gas is kept at 10 liters per minute; on the other hand, the induction refining The vacuum in the steel furnace is kept at 5Pa;
[0033] Keep the heating power of the induction steelmaking furnace at 150KW;
[0034] Refining time is controlled at 25 minutes;
[0035] Refining is completed, vacuum treatment is completed, and slag is removed;
[0036] Under the protection of argon, the s
Embodiment 2
[0038] Production of Inconel600 superalloy
[0039] In a 2-ton induction steelmaking furnace, use induction heating to melt the Inconel600 molten steel matched in proportion;
[0040] Raise the temperature of molten steel to 1550°C;
[0041] Adding CaO-Al on the surface of molten steel 2 o 3 Refining slag is 50kg; of which: CaO-Al 2 o 3 Medium is 20% Al 2 o 3 ;
[0042] After melting the refining slag, add a vacuum cover for vacuum treatment; during this process: on the one hand, argon gas is supplied to the furnace from the vent plug at the bottom of the refining ladle, and the flow rate of argon gas is kept at 15 liters per minute; on the other hand, the induction refining The vacuum in the steel furnace is kept at 5Pa;
[0043] Keep the heating power of the induction steelmaking furnace at 250KW;
[0044] Refining time is controlled at 30 minutes;
[0045] Refining is completed, vacuum treatment is completed, and slag is removed;
[0046] Under the protection of arg
Embodiment 3
[0048] Production of Incoloy800H superalloy
[0049] In a 2-ton induction steelmaking furnace, use induction heating to melt the Incoloy800H molten steel matched in proportion;
[0050] Raise the temperature of molten steel to 1600°C;
[0051] Adding CaO-Al on the surface of molten steel 2 o 3 Refining slag is 60kg; of which: CaO-Al 2 o 3 Medium is 15% Al 2 o 3 ;
[0052] After melting the refining slag, add a vacuum cover for vacuum treatment; during this process: on the one hand, argon gas is supplied to the furnace from the vent plug at the bottom of the refining ladle, and the flow rate of argon gas is kept at 20 liters per minute; on the other hand, the induction refining The vacuum in the steel furnace is kept at 10Pa;
[0053] Keep the heating power of the induction steelmaking furnace at 500KW;
[0054] Refining time is controlled at 40min;
[0055] Refining is completed, vacuum treatment is completed, and slag is removed;
[0056] Under the protection of argon
PUM
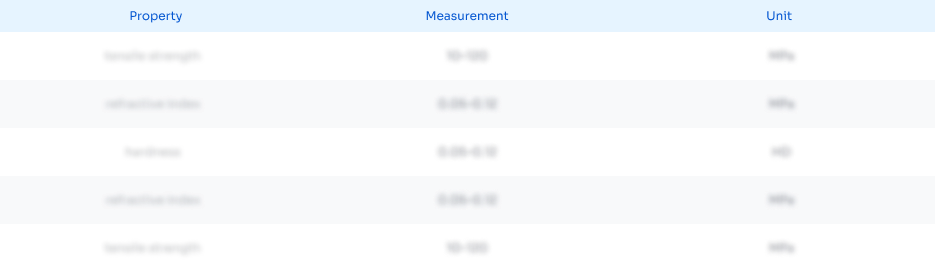
Abstract
Description
Claims
Application Information
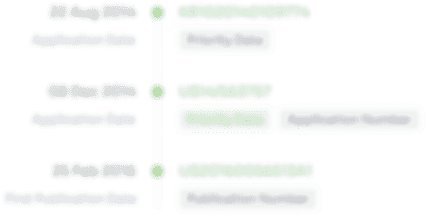
- R&D Engineer
- R&D Manager
- IP Professional
- Industry Leading Data Capabilities
- Powerful AI technology
- Patent DNA Extraction
Browse by: Latest US Patents, China's latest patents, Technical Efficacy Thesaurus, Application Domain, Technology Topic.
© 2024 PatSnap. All rights reserved.Legal|Privacy policy|Modern Slavery Act Transparency Statement|Sitemap