Method and equipment for manufacturing potassium manganate
A technology for the production of potassium manganate and equipment, which is applied in the field of production of potassium manganate, can solve the problems of rare purchase and high price, and achieve the effects of environmental protection, low production cost, significant economic effect and social significance
- Summary
- Abstract
- Description
- Claims
- Application Information
AI Technical Summary
Benefits of technology
Problems solved by technology
Method used
Image
Examples
Embodiment 1
[0031] See Figure 1 and Image 6 , the method for producing potassium manganate of the present invention comprises carrying out gas-liquid concurrent flow oxidation treatment to the mixture of silicomanganese-rich ore powder and potassium hydroxide solution with oxygen-containing gas at high temperature, and its steps are as follows:
[0032] A. Heating the potassium hydroxide solution with a concentration of 60%-79% to 230°C-260°C, and transporting the potassium hydroxide solution into a three-phase circulation bubble reactor through a material pump;
[0033] B. The silicon-manganese-rich ore powder is corrected by silicon-calcium ingredients, and then added to a potassium hydroxide solution with a concentration of 5%-18% to prepare a manganese slurry, and then preheated to 80°C-90°C, and pumped by a material pump The manganese slurry is transported to a three-phase circulation bubble reactor; the weight ratio of the silicomanganese-rich ore powder to the potassium hydroxide sol
Embodiment 2
[0052] This embodiment is an improvement on the basis of Embodiment 1. The equipment and operation steps used in this embodiment are basically the same as those of Embodiment 1, except for the ratio of raw materials;
[0053] In this example, the raw material for preparing manganese slurry is Hunan manganese powder MnO 2 55%, SiO 2 13%, CaO4.5%, activation temperature 215°C. The total weight of CaO used for batching correction is 5% of the manganese powder weight, wherein the CaO accounting for 4% of the manganese powder weight is made into manganese slurry into the reactor with the manganese powder, and the CaO accounting for 1% of the manganese powder weight is added to the sedimentation component as appropriate. in the alkaline barrel.
[0054] Maintain the top pressure of the reactor at 0.45MPa, and the temperature of the reactor at 220°C-230°C. After 4 hours of reaction, part of the feed liquid (4 cubic meters) is released, and then the same amount of manganese slurry an
Embodiment 3
[0057] This embodiment is an improvement on the basis of Embodiment 1. The equipment and operation steps used in this embodiment are basically the same as those of Embodiment 1, except for the ratio of raw materials;
[0058] In this example, the raw material for deploying manganese slurry is Guizhou manganese powder MnO 2 50%, SiO 2 12.5%, CaO7.5%, activation temperature 206°C.
[0059] Keep the reactor top pressure at 0.40 MPa, and the reactor temperature at 210°C-220°C. After 4 hours of reaction, a part (4 cubic meters) of feed liquid is released, and the same amount of manganese slurry and alkali are added. The molar mass ratio of manganese powder, silicon and calcium is close to balance. No need to add milk of lime when manganese slurry is prepared or in the alkali separation tank.
[0060] Effect: The feed liquid discharged from the reactor contains K 2 MnO 4 38%, MnO 2 1.85% MnO 2 The conversion rate is 90%, and the characteristics of soluble potassium silicate a
PUM
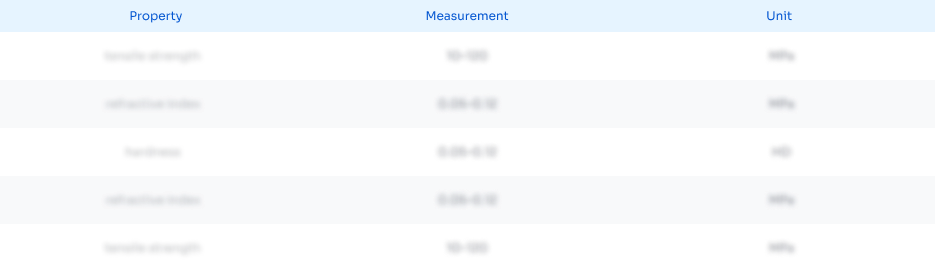
Abstract
Description
Claims
Application Information
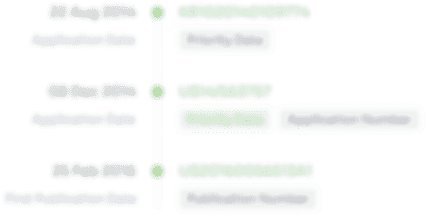
- R&D Engineer
- R&D Manager
- IP Professional
- Industry Leading Data Capabilities
- Powerful AI technology
- Patent DNA Extraction
Browse by: Latest US Patents, China's latest patents, Technical Efficacy Thesaurus, Application Domain, Technology Topic.
© 2024 PatSnap. All rights reserved.Legal|Privacy policy|Modern Slavery Act Transparency Statement|Sitemap