Method for manufacturing cutting line of electrical discharge machine
A machine cutting wire and electric discharge machining technology, which is applied in the direction of electrode manufacturing, electric processing equipment, processing electrodes, etc., can solve the problems of low cutting efficiency, poor effect, easy fragmentation or breakage of cutting wire, etc.
- Summary
- Abstract
- Description
- Claims
- Application Information
AI Technical Summary
Problems solved by technology
Method used
Image
Examples
Embodiment Construction
[0017] The present invention is a manufacturing method of electric discharge machine cutting wire. The main step is to form a metal alloy. The alloy can be made of brass or steel as the main core, and it can also be used in three parts such as pure copper, brass or copper-clad steel. Different materials directly form the core to form a relatively stable core of the processing line, and then electroplating or inclusion methods are used to form a β-phase brass cladding layer with a zinc content of about 5% to 45% of the specific gravity, while In order to make the EDM cutting wire cut more efficiently, γ-phase brass has a high composition of zinc, with an average specific gravity of about 65%. However, because the γ-phase alloy is extremely fragile, it is almost impossible to cold draw it. The γ-phase alloy material will break and recombine during cold drawing. Therefore, before cold drawing, the γ-phase coating is coated with a thinner layer of brass core by immersion plating or el
PUM
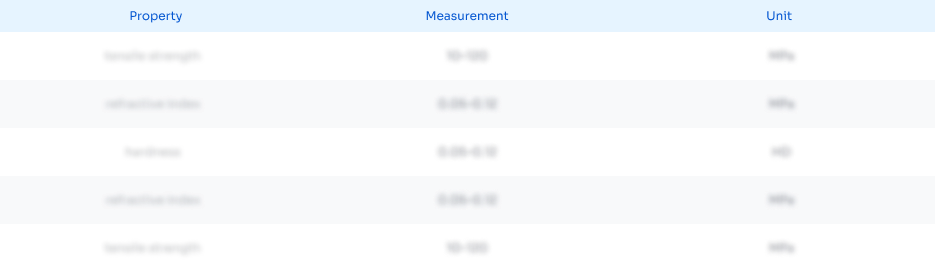
Abstract
Description
Claims
Application Information
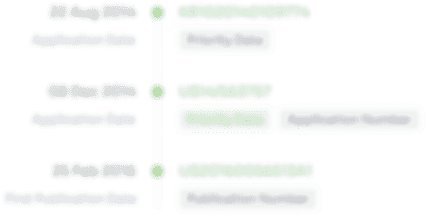
- R&D Engineer
- R&D Manager
- IP Professional
- Industry Leading Data Capabilities
- Powerful AI technology
- Patent DNA Extraction
Browse by: Latest US Patents, China's latest patents, Technical Efficacy Thesaurus, Application Domain, Technology Topic.
© 2024 PatSnap. All rights reserved.Legal|Privacy policy|Modern Slavery Act Transparency Statement|Sitemap