Processing method for preparing imidacloprid wettable powder from crude imidacloprid
A wettable powder, processing method technology, applied in the directions of botanical equipment and methods, biocides, animal repellants, etc., can solve the problems of difficult processing of imidacloprid crude oil and high processing costs, and achieve low processing costs and simple processes. Effect
- Summary
- Abstract
- Description
- Claims
- Application Information
AI Technical Summary
Benefits of technology
Problems solved by technology
Method used
Examples
Embodiment 1
[0007] First add 120 kg of 200-mesh white carbon black to the gravity-free mixer, then add 240 kg of 60°C imidacloprid crude oil just out of the upstream section at one time, start the mixer, and mix for 30 to 50 minutes. The imidacloprid crude oil must be added while it is hot, because when the temperature is above 50°C, it is a homogeneous oily liquid, which is conducive to the adsorption and dispersion of the crude oil by the filler. When the temperature drops to room temperature, it will gradually precipitate hard lumps, which is not conducive to subsequent processing. After being fully mixed by a gravity-free mixer, stop mixing, and add 15 kg of cleaning agent LS, 20 kg of dispersant sodium lignosulfonate, and 105 kg of kaolin into the mixer. Start the mixer and mix for 30-50 minutes. The mixed powder is sieved through a 40-mesh vibrating sieve. The sieved powder is sent to the jet mill for crushing. After passing the inspection, it is sent to the packaging.
Embodiment 2
[0009] First add 200 mesh white carbon black to the trough mixer, then add 50°C imidacloprid crude oil just out of the upstream section at one time, start the mixer, and mix for 30 to 50 minutes. The imidacloprid crude oil must be added while it is hot, because when the temperature is above 50°C, it is a homogeneous oily liquid, which is conducive to the adsorption and dispersion of the crude oil by the filler. When the temperature drops to room temperature, it will gradually precipitate hard lumps, which is not conducive to subsequent processing. After being fully mixed by the trough mixer, stop mixing, and add detergent LS, dispersant sodium lignosulfonate, and kaolin into the mixer. Start the mixer and mix for 30-50 minutes. The mixed powder is sieved through a 40-mesh vibrating sieve. The sieved powder is sent to the jet mill for crushing. After passing the inspection, it is sent to the packaging. Wherein the weight percent of each component is 10% of imidacloprid, 50% of
Embodiment 3
[0011] First add 300-mesh kaolin to the double-helix conical mixer, then add the 50°C imidacloprid crude oil just out of the upstream section at one time, start the mixer, and mix for 30-50 minutes. After being fully mixed by the double-helix conical mixer, stop mixing, and add detergent LS, sodium dodecylbenzenesulfonate, dispersant sodium lignosulfonate, diatomaceous earth, and bentonite into the mixer. Start the mixer and mix for 30-50 minutes. The mixed powder is sieved through a 40-mesh vibrating sieve. The sieved powder is sent to the jet mill for crushing. After passing the inspection, it is sent to the packaging. Wherein the weight percent of each component is 10% of imidacloprid, 40% of kaolin, 5% of detergent LS, 5% of sodium dodecylbenzenesulfonate, 5% of sodium lignosulfonate, 5% of diatomite, 30% of bentonite %.
PUM
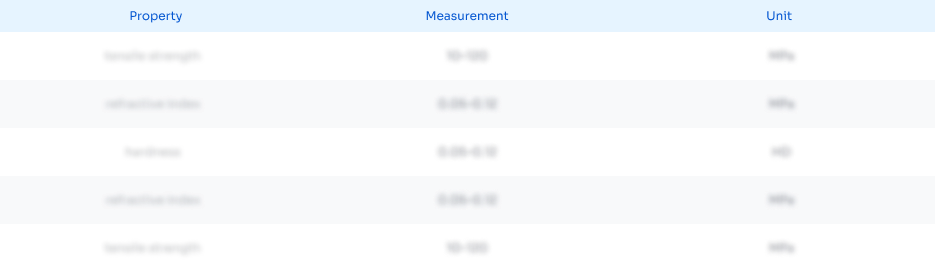
Abstract
Description
Claims
Application Information
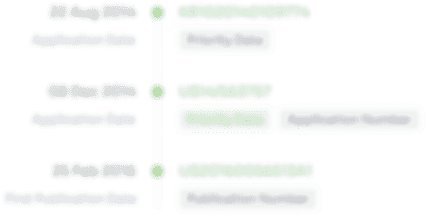
- R&D Engineer
- R&D Manager
- IP Professional
- Industry Leading Data Capabilities
- Powerful AI technology
- Patent DNA Extraction
Browse by: Latest US Patents, China's latest patents, Technical Efficacy Thesaurus, Application Domain, Technology Topic.
© 2024 PatSnap. All rights reserved.Legal|Privacy policy|Modern Slavery Act Transparency Statement|Sitemap