Polyethylene terephthalate (PET)/liquid crystal polymer (LCP) engineering plastics as well as preparation method and application thereof
A technology of engineering plastics and liquid crystal polymers, applied in the field of PET/LCP engineering plastics, can solve the problems of poor performance of PET/LCP engineering plastics, and achieve the effects of high production efficiency, performance improvement, and simple operation
- Summary
- Abstract
- Description
- Claims
- Application Information
AI Technical Summary
Benefits of technology
Problems solved by technology
Method used
Image
Examples
preparation example Construction
[0052] Embodiments of the present invention further provide a method for preparing PET / LCP engineering plastics, comprising the following steps:
[0053] S01, drying the PET resin and the liquid crystal polymer respectively;
[0054] S02, stirring and mixing the dried PET resin and liquid crystal polymer, coupling agent, nucleating agent, antioxidant, lubricant and flame retardant to obtain a PET / LCP engineering plastic precursor;
[0055] S03, mixing the PET / LCP engineering plastic precursor with a filling enhancer, extruding at 250-280°C to obtain a PET / LCP engineering plastic, adding a filling enhancer during the extrusion process,
[0056] The parts by weight of the PET resin, liquid crystal polymer, filling reinforcing agent, coupling agent, nucleating agent, antioxidant, lubricant and flame retardant are as follows:
[0057] Polyethylene terephthalate 30-50
[0058] Liquid crystal polymer 5-20
[0059] Coupling agent 0.2-0.5
[0060] Filling enhancer 30-40
[0
Embodiment 1
[0074] Embodiment PET / LCP engineering plastics of the present invention, comprise the component of following parts by weight:
[0075] 35.5 parts of polyethylene terephthalate, 16.4 parts of liquid crystal polymer, 0.3 parts of γ-glycidyloxypropyl trimethoxysilane, 40 parts of non-alkali coarse-twisted long glass fiber, 0.2 part of CAV 102, 1250 parts of talcum powder 1 part of mesh, 0.2 part of antioxidant 1010, 0.2 part of antioxidant 168, 0.3 part of lubricant TAF, 12 parts of flame retardant PBS-7010, Sb 2 o 3 4 parts.
[0076] The preparation method of PET / LCP engineering plastics of the embodiment of the present invention comprises the following steps:
[0077] a: The polyethylene terephthalate resin and the liquid crystal polymer were air-dried at 130°C and 140°C for 6 hours, respectively;
[0078] b: Use a high-speed mixer to mix lubricant, nucleating agent, flame retardant and antioxidant at high speed, then put it in a drying oven for drying, the drying temperatu
Embodiment 2
[0082] Embodiment PET / LCP engineering plastics of the present invention, comprise the component of following parts by weight:
[0083] 42.8 parts of polyethylene terephthalate, 13.5 parts of liquid crystal polymer, 0.3 parts of γ-glycidyloxypropyl trimethoxysilane, 40 parts of alkali-free coarse twisted long glass fiber, 1020.2 parts of organic nucleating agent CAV, 1 part of inorganic nucleating agent talc powder 1250 mesh, 0.2 part of antioxidant 1010 and 168, 0.3 part of lubricant TAF, 12 parts of flame retardant PBS-7010, Sb 2 o 3 4 parts.
[0084] The preparation method of PET / LCP engineering plastics of the embodiment of the present invention comprises the following steps:
[0085] a: The polyethylene terephthalate resin and the liquid crystal polymer were air-dried at 135°C and 145°C for 5 hours, respectively;
[0086] b: After mixing lubricant, nucleating agent, flame retardant and antioxidant at high speed with a high-speed mixer, put it in a drying oven for dryin
PUM
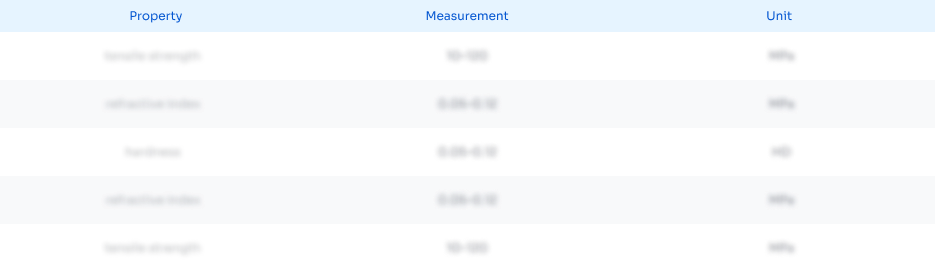
Abstract
Description
Claims
Application Information
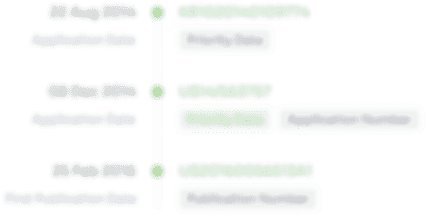
- R&D Engineer
- R&D Manager
- IP Professional
- Industry Leading Data Capabilities
- Powerful AI technology
- Patent DNA Extraction
Browse by: Latest US Patents, China's latest patents, Technical Efficacy Thesaurus, Application Domain, Technology Topic.
© 2024 PatSnap. All rights reserved.Legal|Privacy policy|Modern Slavery Act Transparency Statement|Sitemap