Method for forming amorphous silicon oxide laminated structure
A technology of silicon oxide and stacked structure, which is applied in the direction of electrical components, semiconductor/solid-state device manufacturing, circuits, etc., can solve the problems of high time consumption, impact on production capacity, and low deposition rate, so as to reduce time consumption and increase production capacity Effect
- Summary
- Abstract
- Description
- Claims
- Application Information
AI Technical Summary
Benefits of technology
Problems solved by technology
Method used
Image
Examples
Embodiment Construction
[0031] In the prior art, the reactant used in the deposition process of the amorphous silicon layer is silane, and the reaction temperature is about 560°C; while the reactant used in the deposition process of the silicon oxide layer is silane and nitrogen oxide, and the reaction temperature is about 720°C. The reaction temperature is different, so the amorphous silicon layer and the silicon oxide layer are respectively carried out in different deposition equipment. The semiconductor substrate is repeatedly transferred between two deposition equipments, on which layers of amorphous silicon and silicon oxide are alternately formed.
[0032] figure 2 and image 3 The relationship between the temperature and time of the semiconductor substrate during the formation of the amorphous silicon layer and the silicon oxide layer is given respectively. Such as figure 2 As shown, the formation process of the amorphous silicon layer is mainly divided into three stages: stage I, stage II a
PUM
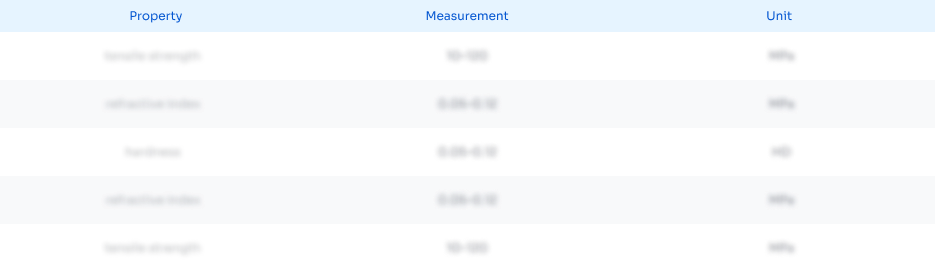
Abstract
Description
Claims
Application Information
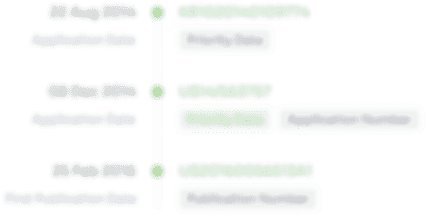
- R&D Engineer
- R&D Manager
- IP Professional
- Industry Leading Data Capabilities
- Powerful AI technology
- Patent DNA Extraction
Browse by: Latest US Patents, China's latest patents, Technical Efficacy Thesaurus, Application Domain, Technology Topic.
© 2024 PatSnap. All rights reserved.Legal|Privacy policy|Modern Slavery Act Transparency Statement|Sitemap