Composite sleeper of prestressed glass reinforced concrete and manufacturing method thereof
A reinforced concrete and prestressing technology, applied in the field of sleepers, can solve the problems such as easy fracturing or breaking of glass steel bars, low shear strength of glass steel bars, failure to achieve prestressing of sleepers, etc., avoiding secondary insulation treatment, insulation and other problems. Good performance and high shear strength
- Summary
- Abstract
- Description
- Claims
- Application Information
AI Technical Summary
Problems solved by technology
Method used
Examples
Example Embodiment
[0044] Example 1
[0045] (1) First coat the two ends of the glass rebar with epoxy resin to form protrusions. When the pressure-resistant material is cured, the anchor end is formed, and then the glass rebar is put into the mold, and 8 pieces The glass steel bar (with an outer diameter of 8mm) is fixed at both ends of the tensioning machine, and then the glass steel bar 2 is stretched. Each glass steel bar 2 bears a tensile force of 20KN. A hoop is installed on the periphery of the prestressed glass steel bar 2. Rib 3. Assemble the sleeper inner core mold and the embedded parts, and then pour concrete into the sleeper inner core mold and vibrate to compact, and then perform curing. When the concrete reaches a predetermined strength, the tension is slowly released The machine pulls the glass steel bar 2 and then cuts the glass steel bar 2 and removes the sleeper inner core mold to obtain the sleeper inner core 1;
[0046] (2) Preliminarily impregnate the glass fiber with rigid foam
Example Embodiment
[0049] Example 2
[0050] (1) The thermosetting phenolic resin is mixed with glass fiber, and then applied to the two ends of the glass rebar to form protrusions. When the pressure-resistant material is cured, the anchor end is formed, and then the glass rebar is placed in the mold Inside, 6 glass steel bars (with an outer diameter of 10mm) are fixed to both ends of the tensioning machine through anchoring ends, and then the glass steel bars 2 are stretched, and the tensile force of each glass steel bar is 30KN. Stirrups 3 are installed on the periphery of the steel bar 2, sleeper inner core molds and embedded parts are assembled, and then concrete is poured into the sleeper inner core mold and vibrated to compact, and then cured. When the concrete reaches a predetermined strength, Slowly release the pulling force of the tensioning machine to the glass rebar 2, and then cut the glass rebar 2 and remove the sleeper inner core mold to obtain the sleeper inner core 1;
[0051] (2) Prel
Example Embodiment
[0055] Example 3
[0056] (1) The unsaturated polyester resin is mixed with basalt fiber, and then coated on the two ends of the glass rebar to form protrusions. When the unsaturated polyester resin is cured, the anchor ends are formed, and then the glass The steel bars are put into the mold, and 4 glass steel bars (outer diameter of 12mm) are fixed to the two ends of the tensioning machine through the anchoring ends, and then the glass steel bars 2 are tensioned. The tensile force of each glass steel bar is 40KN. Stirrups 3 are installed on the periphery of the pre-stressed glass rebar 2, and the sleeper inner core mold and embedded parts are assembled, and then concrete is poured into the sleeper inner core mold and vibrated and compacted, and then cured. When the concrete reaches When the strength is predetermined, slowly release the pulling force of the tensioning machine to the glass rebar 2 and then cut the glass rebar 2 and remove the sleeper inner core mold to obtain the sl
PUM
Property | Measurement | Unit |
---|---|---|
Pull | aaaaa | aaaaa |
Outer diameter | aaaaa | aaaaa |
Abstract
Description
Claims
Application Information
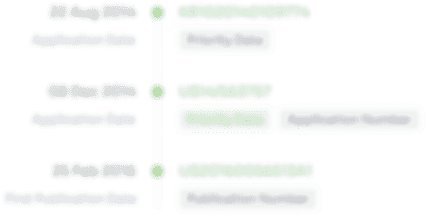
- R&D Engineer
- R&D Manager
- IP Professional
- Industry Leading Data Capabilities
- Powerful AI technology
- Patent DNA Extraction
Browse by: Latest US Patents, China's latest patents, Technical Efficacy Thesaurus, Application Domain, Technology Topic.
© 2024 PatSnap. All rights reserved.Legal|Privacy policy|Modern Slavery Act Transparency Statement|Sitemap