Method for preparing laser thermal composite induction nanoparticle reinforcement laminated film
A technology of nano-particles and enhanced compounding, applied in the coating process of metal materials, coatings, etc., can solve the problems of low interface bonding strength, the size of workpieces polluting the environment, and weak coating interface bonding, etc., to improve the properties and distribution of surface stress , the effect of homogenizing the distribution of nanoparticles and refining the microstructure
- Summary
- Abstract
- Description
- Claims
- Application Information
AI Technical Summary
Problems solved by technology
Method used
Examples
Example Embodiment
[0021] Example 1:
[0022] 1) Select SiC powder with an average size of 10nm for surface treatment;
[0023] 2) Select the ZL104 aluminum alloy substrate to be processed, and polish and polish the surface, and then perform ultrasonic cleaning in alcohol;
[0024] 3) Prepare the nano SiC powder selected in step 1) into an alcohol suspension, then disperse it ultrasonically, and then dip it on the surface of the ZL104 aluminum alloy treated in step 2) at a speed of 5 mm / s, and leave it to dry. ;
[0025] 4) Use nanosecond pulse laser to irradiate the surface of the ZL104 aluminum alloy substrate pre-coated with nano-SiC particles to melt, and the irradiated laser energy density is 0.6 J / cm 2 , The laser pulse width is 10 ns, the spot diameter is 3 mm, so that the nano SiC particles are immersed in the molten pool, and after cooling and solidification, they are half embedded on the surface of the ZL104 aluminum alloy substrate;
[0026] 5) Cover the surface of the ZL104 aluminum alloy su
Example Embodiment
[0031] Example 2:
[0032] 1) Select Al with an average size of 200nm for surface treatment 2 O 3 powder;
[0033] 2) Select the AZ91 Mg alloy substrate to be processed, and polish and polish its surface, and then perform ultrasonic cleaning in alcohol;
[0034] 3) Change the nano Al selected in step 1) 2 O 3 The powder is formulated into an alcohol suspension, then ultrasonically dispersed, and then dip-coated on the surface of the AZ91 Mg alloy treated in step 2) at a speed of 1 mm / s, and left to dry;
[0035] 4) Pre-coated nano-Al with nanosecond pulse laser irradiation 2 O 3 The surface of the granular AZ91 Mg alloy matrix is melted, and the laser energy density is 0.1 J / cm 2 , The laser pulse width is 5 ns, the spot diameter is 10 mm, so that nano Al 2 O 3 The particles are immersed in the molten pool, and half embedded in the surface of the AZ91 Mg alloy matrix after cooling and solidification;
[0036] 5) Use aluminum foil as the absorption layer to cover the nano Al obtained
Example Embodiment
[0041] Example 3:
[0042] 1) Select nano TiN powder with an average size of 80nm for surface treatment;
[0043] 2) Select the aluminum bronze alloy substrate to be processed, and polish and polish its surface, and then perform ultrasonic cleaning in alcohol;
[0044] 3) Prepare the nano TiN powder selected in step 1) into an alcohol suspension, then disperse it ultrasonically, and then dip it on the surface of the aluminum bronze alloy treated in step 2) at a speed of 10 mm / s, and leave it to dry. ;
[0045] 4) Use nanosecond pulse laser to irradiate the surface of aluminum bronze alloy substrate pre-coated with nano-TiN particles to melt, and the laser energy density is 1 J / cm 2 , The laser pulse width is 15 ns, the spot diameter is 6 mm, so that the nano-TiN particles are immersed in the molten pool, and after cooling and solidification, they are half embedded in the surface of the aluminum bronze alloy substrate;
[0046] 5) Use black paint as the absorption layer to cover the su
PUM
Property | Measurement | Unit |
---|---|---|
Laser pulse width | aaaaa | aaaaa |
Spot diameter | aaaaa | aaaaa |
Laser pulse width | aaaaa | aaaaa |
Abstract
Description
Claims
Application Information
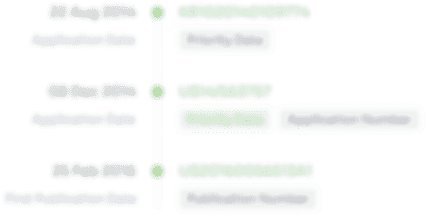
- R&D Engineer
- R&D Manager
- IP Professional
- Industry Leading Data Capabilities
- Powerful AI technology
- Patent DNA Extraction
Browse by: Latest US Patents, China's latest patents, Technical Efficacy Thesaurus, Application Domain, Technology Topic.
© 2024 PatSnap. All rights reserved.Legal|Privacy policy|Modern Slavery Act Transparency Statement|Sitemap