Method for making adhesive film
A manufacturing method and technology for bonding films, which are applied in the direction of film/sheet-like adhesives, adhesives, etc., can solve the problems of reduced workability, inability to stabilize co-extrusion molding, and inability to increase the mixing ratio of tackifying resin, etc. Stable quality and good forming workability
- Summary
- Abstract
- Description
- Claims
- Application Information
AI Technical Summary
Problems solved by technology
Method used
Image
Examples
Example Embodiment
[0058] [Example 1]
[0059] As the thermoplastic resin in the base layer forming material, low-density polyethylene (Nippon Polyethylene Corporation, NOVATEC LD LF547) was used, and as the polyolefin resin in the adhesive layer forming material, polypropylene (Japan POLYCHEM ( Co., Ltd., trade name "NOVATEC PPFX3", melting temperature 139°C, MFR8.0 (according to JIS-K6921-2)), as the thermoplastic elastomer in the adhesive layer forming material, styrene-butadiene- A hydrogenated styrene block copolymer (SEBS, manufactured by Shell Chemical Co., Ltd., trade name "KRATON G1657"). As a tackifying resin in the adhesive layer forming material, a hydrogenated terpene resin (manufactured by Yasuhara Chemical Co., Ltd., Trade name "Clearon P125").
[0060] First, the polyolefin-based resin and the hydrogenated terpene-based resin were melt-mixed according to the mixing ratio shown in Table 1 to prepare pre-kneaded pellets. Then, the pre-kneaded pellets and SEBS were dry-blended in the mixi
Example Embodiment
[0061] [Example 2]
[0062] As the thermoplastic elastomer in the adhesive layer forming material, a hydrogenated styrene-isoprene-styrene block copolymer (SEPS, manufactured by Kuraray Co., Ltd., trade name "Septon 2043") was used instead of SEBS, according to the table The mixing ratio shown in 1 is that polypropylene and hydrogenated terpene-based resin are melt-mixed to produce pre-kneaded pellets, and the pre-kneaded pellets and SEPS are dry-blended according to the mixing ratio shown in Table 1. In addition, with Example 1 was implemented in the same manner, and an adhesive film (2) having a base layer (thickness 100 μm) and an adhesive layer (thickness 15 μm) was produced.
Example Embodiment
[0063] [Example 3]
[0064] As the polyolefin resin in the adhesive layer forming material, low-density polyethylene (melting temperature 110°C, MFR2.0 (according to JIS-K6922-2)) is used instead of polypropylene as the thermoplastic elasticity in the adhesive layer forming material Body, using hydrogenated styrene-isoprene-styrene block copolymer (SEPS, manufactured by Kuraray, trade name "Septon 2043") instead of SEBS as the tackifying resin in the adhesive layer forming material, Use hydrogenated aromatic petroleum resin (manufactured by Arakawa Chemical Industry Co., Ltd., trade name "ARCON P-125") instead of hydrogenated terpene resin, and compare low-density polyethylene with hydrogenated aromatic resin according to the mixing ratio shown in Table 1. The petroleum resin was melt-mixed to prepare pre-kneaded pellets, and the pre-kneaded pellets and SEPS were dry-blended according to the mixing ratio shown in Table 1. Except for this, the same procedure as in Example 1 was carri
PUM
Property | Measurement | Unit |
---|---|---|
Thickness | aaaaa | aaaaa |
Thickness | aaaaa | aaaaa |
Thickness | aaaaa | aaaaa |
Abstract
Description
Claims
Application Information
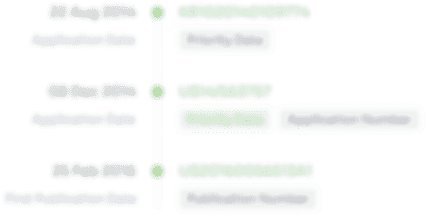
- R&D Engineer
- R&D Manager
- IP Professional
- Industry Leading Data Capabilities
- Powerful AI technology
- Patent DNA Extraction
Browse by: Latest US Patents, China's latest patents, Technical Efficacy Thesaurus, Application Domain, Technology Topic.
© 2024 PatSnap. All rights reserved.Legal|Privacy policy|Modern Slavery Act Transparency Statement|Sitemap