Method adopting stereoscopic metal belt technology for producing thermal pressure-sensitive resistor and products thereof
A technology of piezoresistor and thermistor chip, applied in piezoresistor cores, piezoresistors, resistors, etc., can solve the problems of low work efficiency, large space requirement, easy deformation of lead wires, etc., and achieve work efficiency Improve welding efficiency and solve the effect of easy slag drop
- Summary
- Abstract
- Description
- Claims
- Application Information
AI Technical Summary
Problems solved by technology
Method used
Image
Examples
Embodiment 1
[0038] Embodiment 1 of the present invention: the three-dimensional metal strip process is used to produce thermal varistors, and the three pins used for welding the thermal varistors are made of the same tinned steel strip (hereinafter referred to as the steel strip). The thickness of the three pins is 0.3mm, and the three pins are fixed on the steel strip to form a three-dimensional structure, that is, the horizontal spacing and longitudinal structure of the three pins are completely consistent with the spatial structure of the pins of the finished thermal varistor, such as figure 1 , figure 2 As shown; directly plug the three pins fixed on the steel strip with the thermistor chip and the varistor chip, so that each pin is in the corresponding position of the thermistor chip and the varistor chip, wherein, The common terminal pin is inserted between the thermistor chip and the varistor chip; while soldering the three pins, the thermistor chip and the varistor chip are soldere
Embodiment 2
[0040]Embodiment 2 of the present invention: the three-dimensional metal strip process is used to produce thermal varistors, and the three pins used for welding the thermal varistors are made of the same tinned iron strip (hereinafter referred to as the iron strip). The thickness of the varistor is 0.3mm, and the three pins are fixed on the iron strip to form a three-dimensional structure, that is, the horizontal spacing and vertical spacing of the three pins are completely consistent with the spatial structure of the pins of the finished thermal varistor. Figure 5 , Figure 6 As shown; first, eccentrically couple the thermistor chip and the piezoresistor chip, and reserve enough space on the piezoresistor chip for subsequent soldering of the common terminal pins, and then connect the three pins fixed on the iron strip The pins are inserted into the thermistor chip and the piezoresistor chip, so that each pin is in the corresponding position of the thermistor chip and the piezor
Embodiment 3
[0042] Embodiment 3 of the present invention: The three-dimensional metal strip process is used to produce thermal varistors, and the three pins used for welding thermal varistors are made of the same tinned copper strip (hereinafter referred to as copper strip). The thickness of the three pins is 0.3mm, and the three pins are fixed on the copper strip to form a three-dimensional structure, that is, the horizontal spacing and vertical spacing of the three pins are completely consistent with the spatial structure of the pins of the finished thermal varistor. Such as Figure 5 , Figure 6 As shown in the figure below; first, eccentrically couple the thermistor chip and the varistor chip, and reserve enough space on the varistor chip for subsequent soldering of the common terminal pins, and then connect the three pins fixed on the copper tape The pins are inserted into the thermistor chip and the piezoresistor chip, so that each pin is in the corresponding position of the thermisto
PUM
Property | Measurement | Unit |
---|---|---|
Thickness | aaaaa | aaaaa |
Thickness | aaaaa | aaaaa |
Surface area | aaaaa | aaaaa |
Abstract
Description
Claims
Application Information
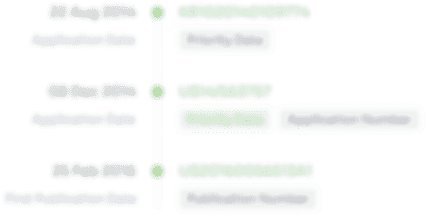
- R&D Engineer
- R&D Manager
- IP Professional
- Industry Leading Data Capabilities
- Powerful AI technology
- Patent DNA Extraction
Browse by: Latest US Patents, China's latest patents, Technical Efficacy Thesaurus, Application Domain, Technology Topic.
© 2024 PatSnap. All rights reserved.Legal|Privacy policy|Modern Slavery Act Transparency Statement|Sitemap