Preparation method of graphite sheet surface chemical plating iron-nickel alloy layer
A surface chemistry, graphite sheet technology, applied in the field of chemical plating, can solve the problem of unsatisfactory electromagnetic shielding performance, and achieve the effects of excellent electromagnetic comprehensive performance, low cost, and dense and uniform coating.
- Summary
- Abstract
- Description
- Claims
- Application Information
AI Technical Summary
Benefits of technology
Problems solved by technology
Method used
Image
Examples
example 1
[0028] 1 Pretreatment process of graphite flakes
[0029] 1.1 Oil removal process Take 1g of graphite flakes with a diameter of 80-100um and a thickness of 5-20um, put them into 100ml of NaOH aqueous solution with a mass fraction of 100g / L, and fully stir in a constant temperature magnetic stirrer to disperse (temperature is 45°C, the time is 2h, the stirring speed is 300r / min). After stirring, wash with deionized water for 3 to 5 times to neutrality, filter, and finally put it into a drying oven at 80° C. for 4 hours to dry for later use.
[0030] 1.2 Oxidation process Prepare 100ml of H2SO4 solution with a volume fraction of 250ml / L, add 10g of K 2 Cr 2 o 7 , stirred at room temperature (25°C) for 10 min to dissolve completely. Add the graphite flakes obtained in step 1.1 into the prepared solution, and fully stir in a constant temperature magnetic stirrer to disperse (temperature is 60°C, time is 10min, stirring speed is 300r / min). After stirring, wash with deioni
example 2
[0037] 1 Pretreatment process of graphite flakes
[0038] 1.1 Degreasing process Take 1g of graphite flakes with a diameter of 80-100um and a thickness of 5-20um, put them into 100ml of NaOH aqueous solution with a mass fraction of 80g / L, and fully stir in a constant temperature magnetic stirrer to disperse (temperature is 40°C, the time is 3h, the stirring speed is 300r / min). After stirring, wash with deionized water for 3 to 5 times to neutrality, filter, and finally put it into a drying oven at 80° C. for 4 hours to dry for later use.
[0039] 1.2 Oxidation process Prepare 100ml of H2SO4 solution with a volume fraction of 200ml / L, add 15g of K 2 Cr 2 o 7 , stirred at room temperature (25°C) for 10 min to dissolve completely. Add the graphite flakes obtained in step 1.1 into the prepared solution, and fully stir in a constant temperature magnetic stirrer to disperse (temperature is 50°C, time is 15min, stirring speed is 300r / min). After stirring, wash with deionize
PUM
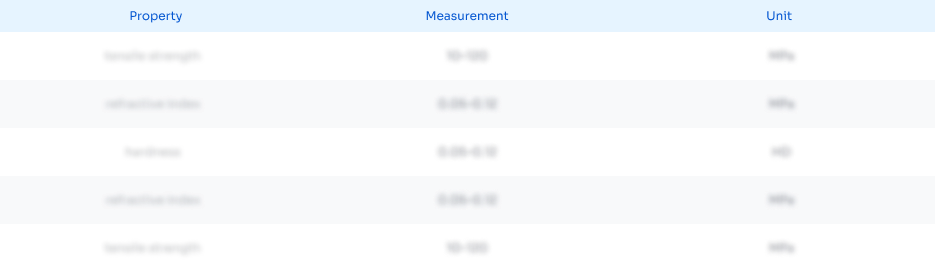
Abstract
Description
Claims
Application Information
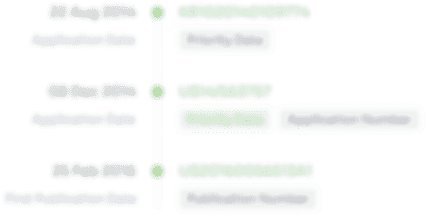
- R&D Engineer
- R&D Manager
- IP Professional
- Industry Leading Data Capabilities
- Powerful AI technology
- Patent DNA Extraction
Browse by: Latest US Patents, China's latest patents, Technical Efficacy Thesaurus, Application Domain, Technology Topic.
© 2024 PatSnap. All rights reserved.Legal|Privacy policy|Modern Slavery Act Transparency Statement|Sitemap