Left and right convex-mold die-forging process
A technology of convex model and convex die, which is applied in the direction of swage forging presses, manufacturing tools, upsetting forging presses, etc., can solve problems such as difficult to meet die forging requirements, affect processing accuracy, reduce die forging efficiency, etc., and achieve improved material quality. Utilization rate, good applicability, and the effect of improving mechanical properties
- Summary
- Abstract
- Description
- Claims
- Application Information
AI Technical Summary
Benefits of technology
Problems solved by technology
Method used
Image
Examples
Embodiment 1
[0017] figure 1 with figure 2 A specific embodiment of the invention is shown in which figure 1 is a flow chart of the present invention; figure 2 It is a schematic diagram of the left punch in the present invention.
[0018] See figure 1 with figure 2 , a left and right convex mold forging process, including an upper die, a lower die and a multi-directional die forging hydraulic press, the vertical cylinder of the multi-directional die forging hydraulic press is connected with the upper die, and also includes a left convex die and a right convex die. die, the left punch and the right punch both include a holder pressure pad 1, a punch holder 2 and a punch body 3, and the punch body is fixed in the punch holder and fixed on the On the horizontal side cylinder 4 of the multi-directional die forging hydraulic press, the process includes the following steps:
[0019] Step A, use the heater to preheat the upper die, lower die, left punch and right punch, so that the preheati
PUM
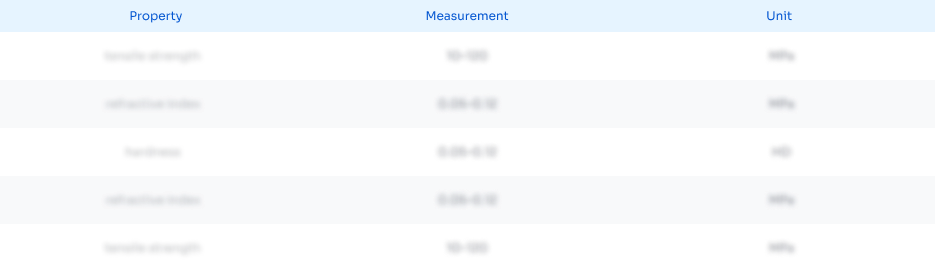
Abstract
Description
Claims
Application Information
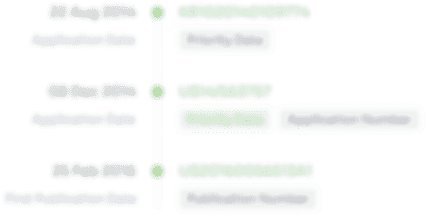
- R&D Engineer
- R&D Manager
- IP Professional
- Industry Leading Data Capabilities
- Powerful AI technology
- Patent DNA Extraction
Browse by: Latest US Patents, China's latest patents, Technical Efficacy Thesaurus, Application Domain, Technology Topic.
© 2024 PatSnap. All rights reserved.Legal|Privacy policy|Modern Slavery Act Transparency Statement|Sitemap